Rob Clemson, Technical Director
Flamco (now incorporated into Aalberts hfc)
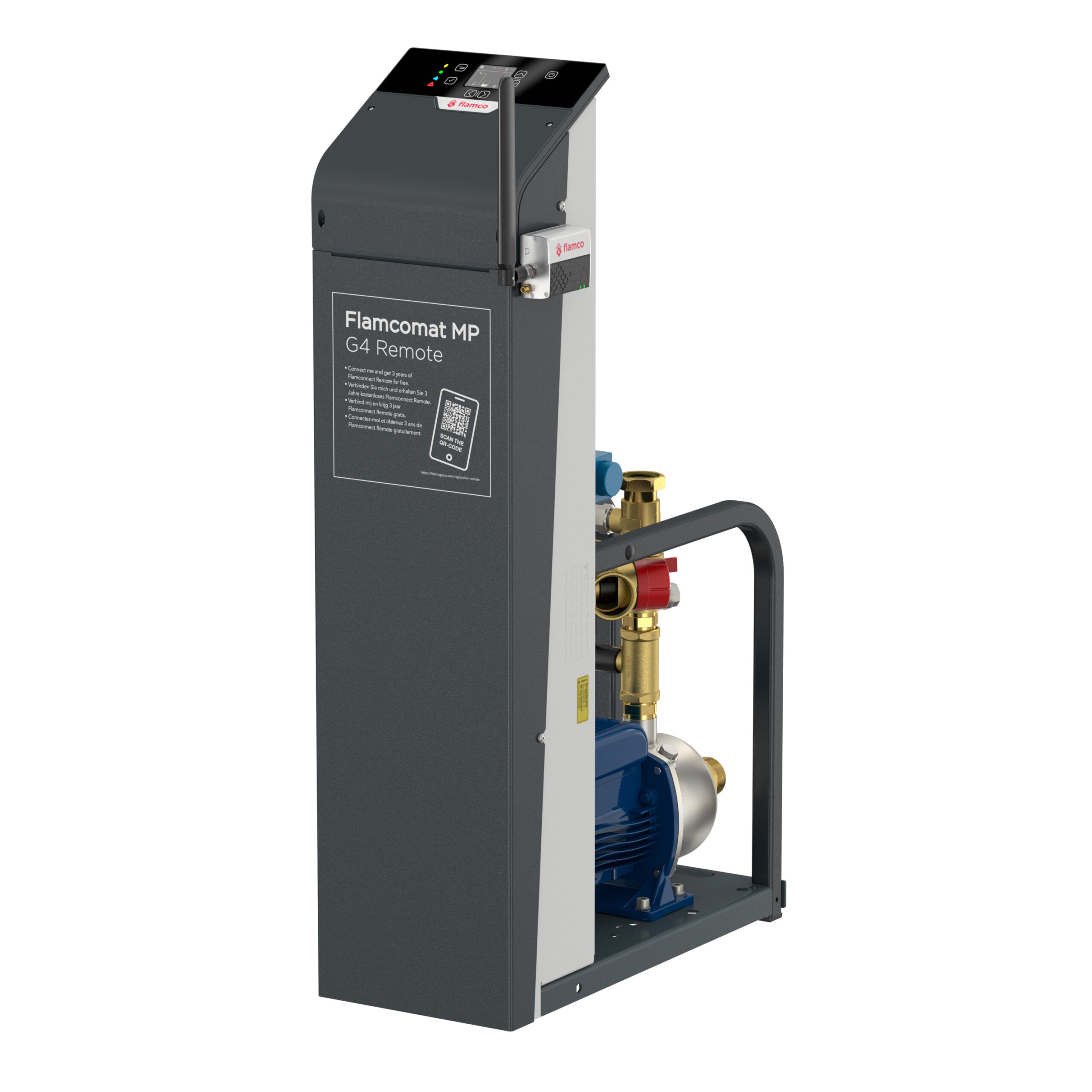
The importance of pressurisation equipment
Rob Clemson*, Technical Director at Aalberts Hyrdonic Flow Control UK (now incorporating Flamco) puts the spotlight on pressurisation, top-up, and water makeup in sealed heating and cooling systems.
The design and sustainability of sealed system heating and cooling systems hinge on many critical elements. While few systems are built with failure in mind, too often the design approach neglects an integrated strategy that ensures all components work in harmony.
This oversight can compromise efficiency, longevity, and overall system reliability. To fully appreciate the value of pressurisation equipment and water makeup, it is helpful to think of a sealed hydronic system as analogous to a human body: every component must work seamlessly together to ensure the survival of the whole.
Viewing a sealed hydronic system as a human body brings to light relatable operational principles:
- The Building Management System (BMS) functions as the brain, controlling and monitoring system activities.
- The circulation pump acts as the heart, propelling water through the system to maintain flow and distribution.
- The pipework serves as the arteries and veins, transporting water throughout the structure.
- The air separation equipment functions as lungs removing unwanted gas
- The filtration performs the same role as kidneys, removing unwanted particulate
- The pressurisation (we can also consider this as ‘topup’) provides essential fluid to overcome leaks and system venting
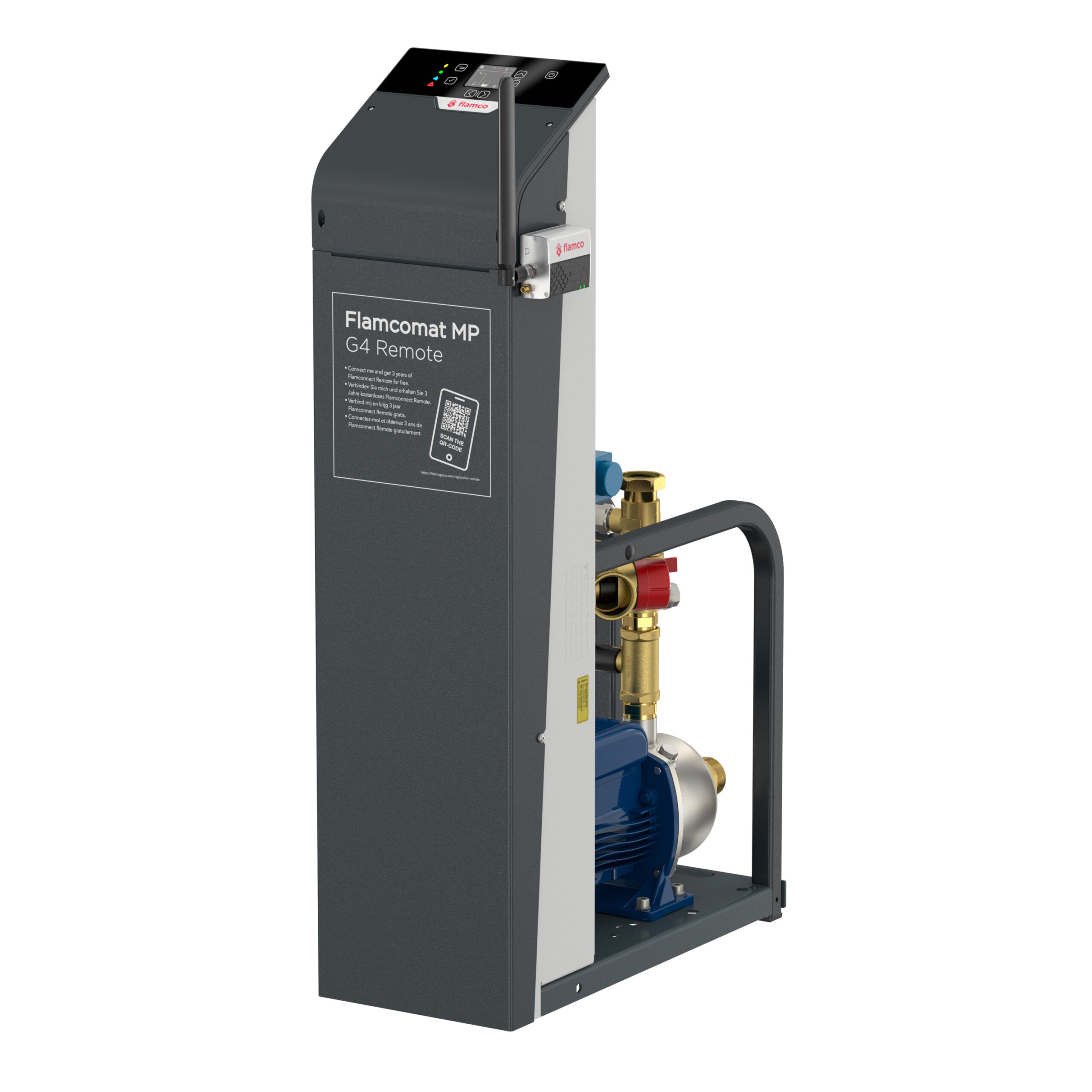
However, at the centre of this intricate ecosystem lies the most critical component: water, the life blood of the system. Industry standards such as BG29, BG50, and VDI2035 emphasize water quality, but the importance of pressurisation — maintaining the right balance and control of water pressure — is frequently overlooked. This oversight can lead to inefficiencies, unwanted down time and premature system failures.
The role of pressurisation equipment
Pressurisation equipment is essential for the long-term performance of a closed heating or cooling system. Maintaining correct system pressure prevents issues such as cavitation, water lock, air ingress and consequential damage to vital components.
The responsibility for designing a reliable pressurisation system can be complex and may fall to different parties: consultants, contractors, or equipment manufacturers may all have a role. BSRIA’s BG82* provides comprehensive guidance on pressurisation, serving as a critical resource for industry professionals.
System criticality and design considerations
Sealed systems are mission-critical. Failure can disrupt not only the thermal comfort of a building but also essential operations e.g. cooling is essential in data centres; lack of water in a healthcare environment can have a devastating knock-on effect.
The selection of pressurisation and expansion equipment must be made with an understanding of the following factors:
- Type of system and critical needs: Tailored approaches are needed based on system size, pressure demands, and installation environment
- Installation location and space constraints: The physical space available for pressurisation equipment may influence design choices
- Compatibility of technologies: Ensuring that standalone pressurisation units and degassing equipment can operate in harmony with the rest of the system is essential for maintaining consistent pressure and system integrity
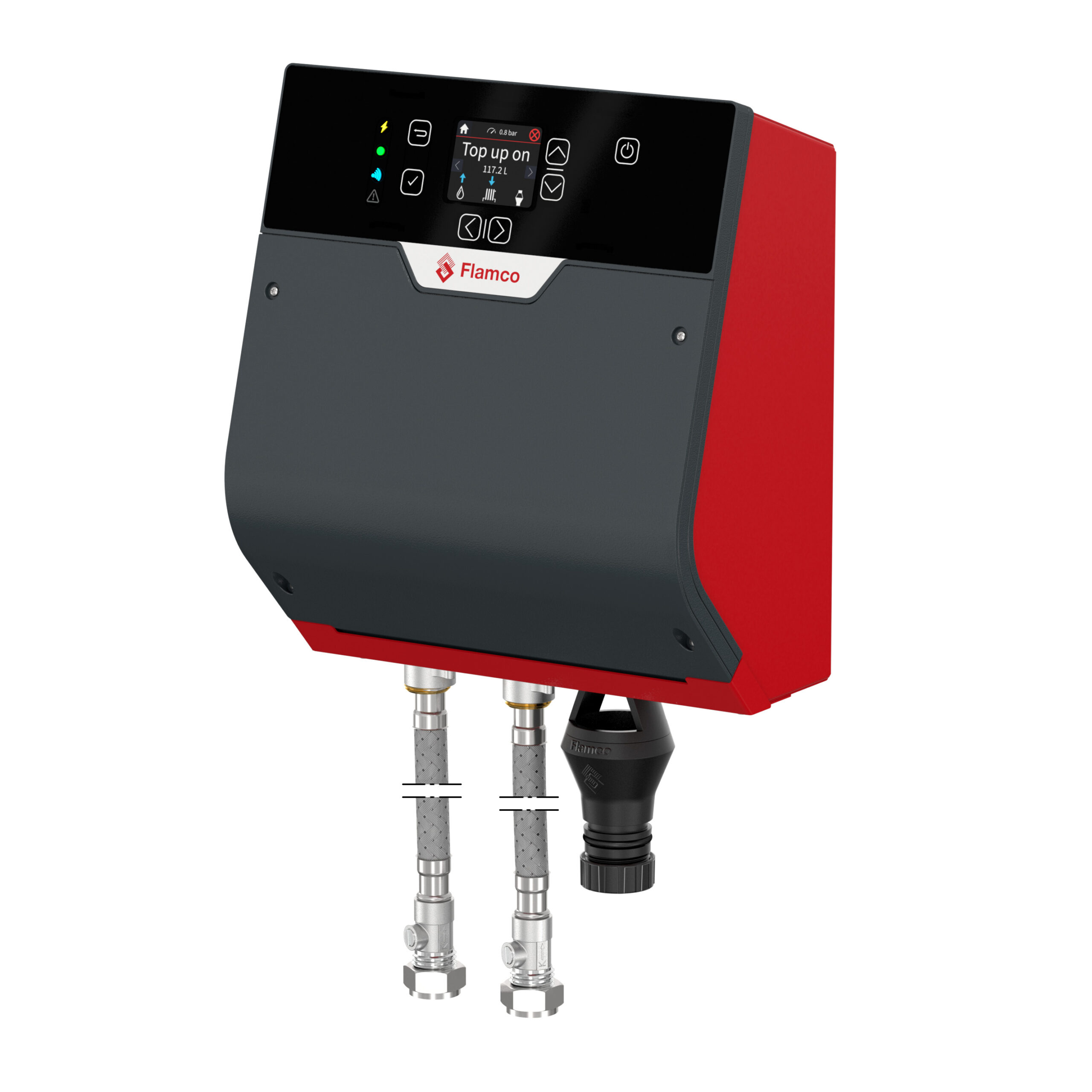
Historical perspective and evolution
Sealed systems date back to the late 1960s, when expansion vessel technology was introduced. By the 1980s, commercial systems began to incorporate automatic water top-up mechanisms, laying the groundwork for today’s advanced pressurisation units. Initially, these units served a straightforward purpose: holding a reserve of water at a pressure higher than the system’s static needs, controlled by a pressure-reducing valve.
In modern applications, pressurisation equipment has evolved. It is no longer sufficient for units to simply maintain pressure; they now monitor system status, prevent misuse, and integrate with building management systems (BMS) to provide feedback and alerts. Furthermore, these units must comply with stringent water regulations and provide clear visibility of air gaps, when being used, to meet the requirements of water authority inspections.
Health and safety considerations
Health and safety remain paramount in modern system design. The presence of stored water in warm plant rooms, as seen in break tanks within pressurisation units, poses a perceived risk of Legionella contamination.
Although water in these tanks is not intended for consumption, neglecting to assess the risk can lead to health hazards. Recent technological advancements address these concerns, incorporating features to minimize the potential for Legionella growth within pressurisation equipment. This includes designing systems with reduced water storage volumes and venting protocols for the supply ‘dead leg.’
Conclusion
In conclusion, while pressurisation equipment may have historically been an afterthought, it is now clear that it plays an indispensable role in the functionality and longevity of sealed heating and cooling systems.
The focus must shift towards a holistic design approach that includes pressurisation as an integral part of system planning. With evolving expectations for form and function, as well as increasing attention to health and safety, the industry must prioritize this critical element during the initial design phase to ensure sustainable, reliable, and visually appealing installations. By considering the importance of pressurisation and expansion from the outset, the industry can better design systems that are not only efficient and compliant but also built to last, serving as benchmarks for modern engineering excellence.
Rob Clemson is also the author of the BSRIA Guide BG82/2022, ‘Pressurisation of Closed Heating and Cooling Systems’.