Mark Harrison, Commercial Director
Firesafe Fire Rated Ductwork Ltd
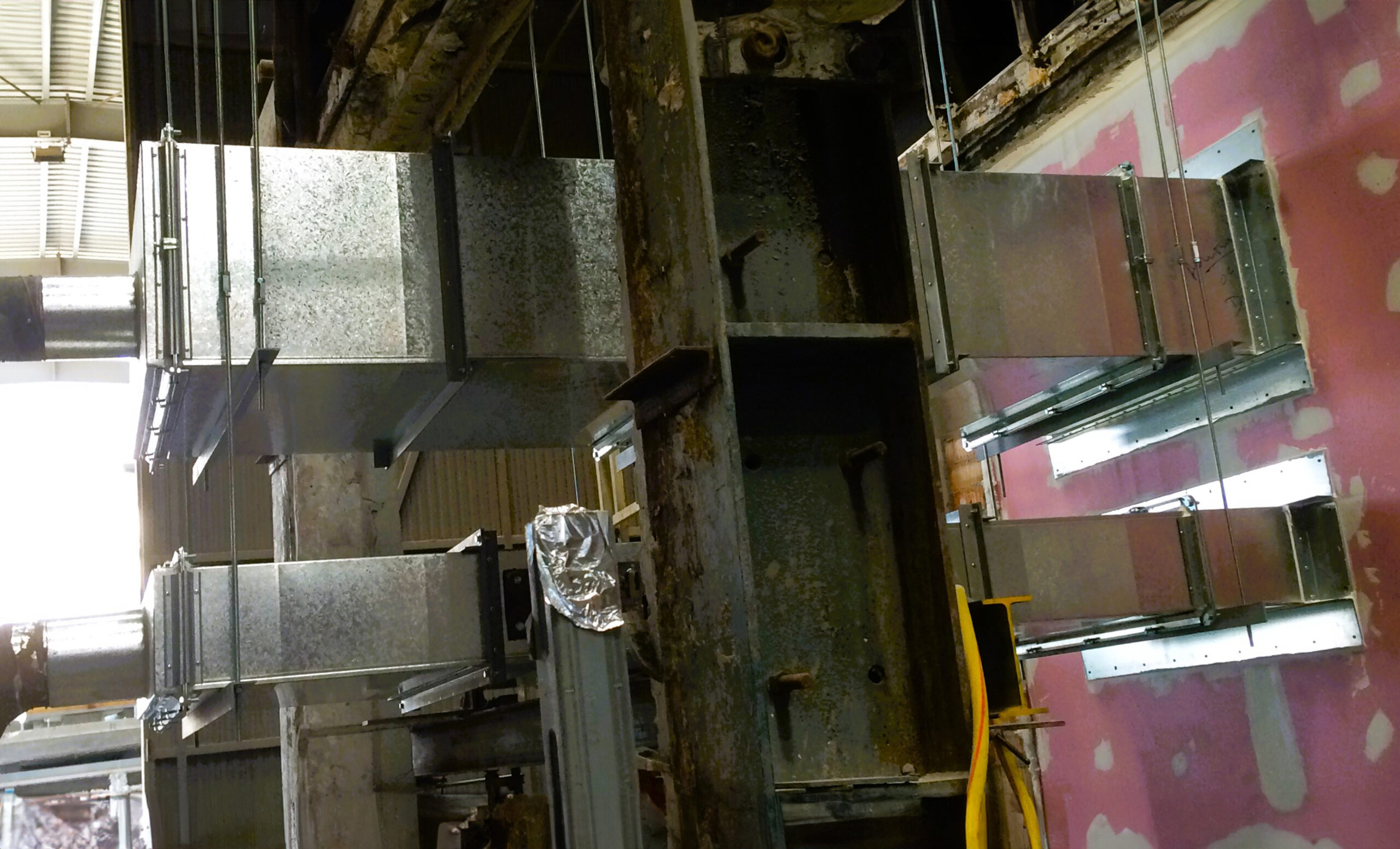
Climate change having a major impact on seals
Mark Harrison, Firesafe Fire Rated Ductwork Commercial Director and BSI FSH 22-9 Chair, surveys the changing climate urged by the Hackitt Report and highlights some practices which still need to be widely adopted
“The culture must change to one where the participants at all levels focus on delivering the required quality.”
This was a key message in the Hackitt Report summary. It reflects the level of engagement and attention to detail required by all involved to improve fire safety in buildings. Solutions to all construction related problems can be found, provided sufficient time and planning goes into the design. A ‘make do’ approach cannot be accepted.
Since our previous Technical Editorial , “Performing Seals” was published in 2021, we have seen a major shift in the climate surrounding the importance of correctly specifying, constructing and completing penetration seals for fire resisting ducts.
This is encouraging, yet more still needs to be done. Consideration should be given as early as the Spatial Coordination stage (RIBA Plan of Works S3) to ensure sufficient space for, and better coordination of, services. This would advance the use of tested penetrations, as opposed to an engineered judgement of an untested detail.
‘As tested’
In terms of fire compartmentation, fire resisting ductwork provides the same level of protection to a building as a fire damper and, as such, the penetration needs to be treated with the same level of scrutiny and care to which a tested and inspected fire damper would be subjected.
Standard non-fire resisting ductwork systems utilise fire dampers to prevent the passage of fire and smoke (if classified for smoke) from one compartment to another in a building. This is described in BS9999 as Method 1 (thermally actuated) and Method 4 (automatically actuated).
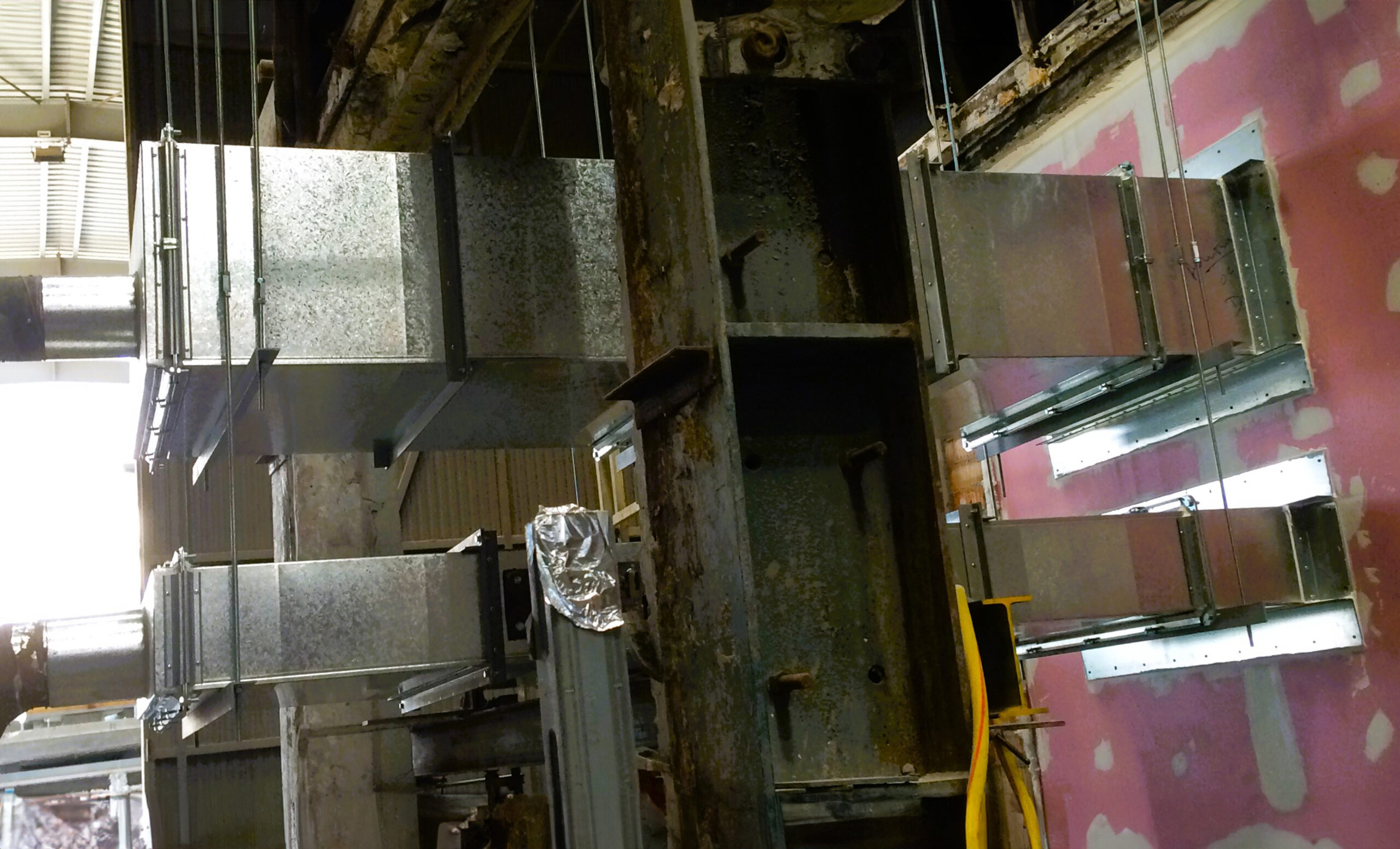
BS9999 Clause 32.5.2.6 ‘Fire stopping of ducts and dampers’ also states:
“The junction between the air-handling system and the wall or floor should be sealed to maintain the fire resistance of the element in which the system is installed. To ensure that systems are compatible, only penetration seals that have been tested or assessed in conjunction with the duct or damper should be used.”
Manufacturers of fire resisting ducts have fully tested penetration details encompassing varying levels of performance in different wall and floor constructions.
It is critical that these elements are considered early in the design phases to ensure adequate space and compatible construction methods are selected to enable ‘as tested’ details to be used, in accordance with BS9999.
To achieve an ‘as tested’ penetration detail, the openings in the fire-separating elements must be formed exactly as per the manufacturers’ details. Any deviation from these details will result in the penetration not being certified as part of the ductwork installation. An alternative fire stopping method would then need to be agreed with the Responsible Person, aka the Authority Having Jurisdiction (AHJ).
Design Stages
The importance of the design stages cannot be understated. Architects have a major role to play in making the shift away from bespoke, some might say ad-hoc, arrangements to ‘as tested’ details.
For decades, the building services sector has struggled to work in limited spaces where there has been little consideration for how an installation is going to be achieved in a compliant manner.
The reality is that fire resisting ducts need the same installation space as a fire damper; but this is largely not recognised.
Test Standards do not permit the testing of a duct fitted tight to the underside of the slab.
As a minimum, 500mm space is required from the top of the duct to the underside of the furnace roof.
(See diagram).
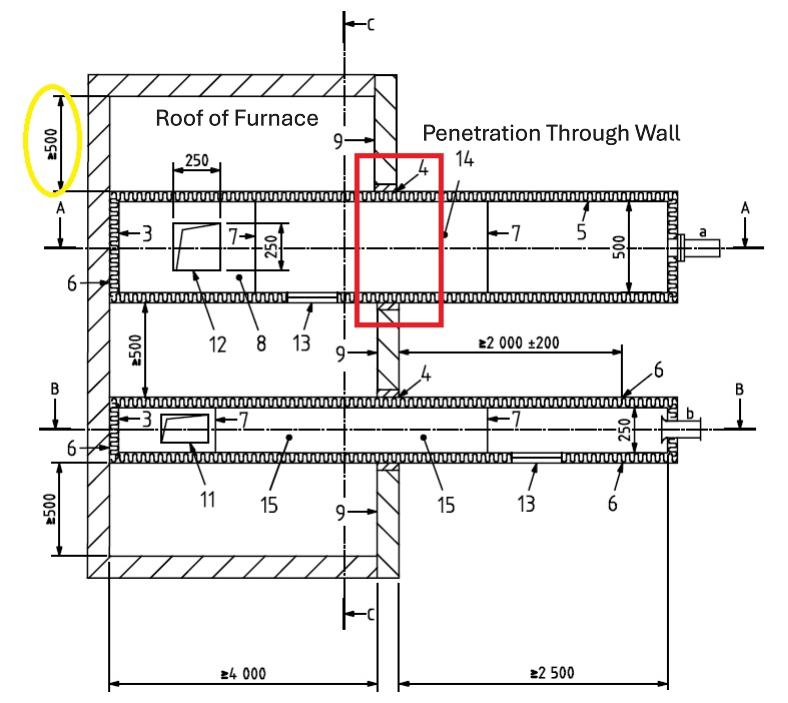
This means all manufacturers will have tested a 4-sided penetration detail, but how often do we see ductwork installed tight to the underside of the soffit with the opening in the wall having no lintel / top edge against which a seal can be formed?
What are the main factors to be considered at design stage?
- Early engagement with the fire resisting duct manufacturer
- Openings are to be specific for the duct and not any other services / dampers, unless tested in a multi-service arrangement
- The annular space around the duct must not be greater than specified in the tested arrangement. It may be acceptable for this space to be smaller but this should be checked with the manufacturer
- The wall and / or floor must be constructed and classified in a manner that satisfies the required fire performance and must match the classification of the ductwork.
For example, if ducts are tested in flexible partitions (plasterboard or similar) they can also be used in masonry or concrete but not visa-versa, unless tested in both types of construction
- There must be adequate space around the duct to allow the installation of the fire stopping system, which could be steel plates, insulation material, plasterboard pattresses and the like
If the structural opening does not satisfy the requirements of the manufacturer’s tested arrangement there will need to be an alternative solution put forward by a fire stopping specialist in collaboration with the ductwork Manufacturer, Contractor and Responsible Person.
Who is responsible for certifying Penetrations?
To avoid the risk of unqualified or insufficiently competent persons being involved in this critical aspect of fire safety, we would suggest there are only two possibilities in terms of responsibility for the inspection and certifying of fire penetrations:
- The ductwork manufacturer for ‘as tested’ details (even if installation is being undertaken by a 3rd party) or,
- A fire stopping specialist appointed to provide an alternative bespoke solution to the approval of the AHJ.
Labelling of Penetrations
As stated earlier, fire resisting ductwork penetrations should be treated in the same manner as fire dampers, with a unique identification reference included on the ‘as fitted’ drawings.
There needs to be a formal inspection regime at various stages of the installation, with records kept verifying each penetration.
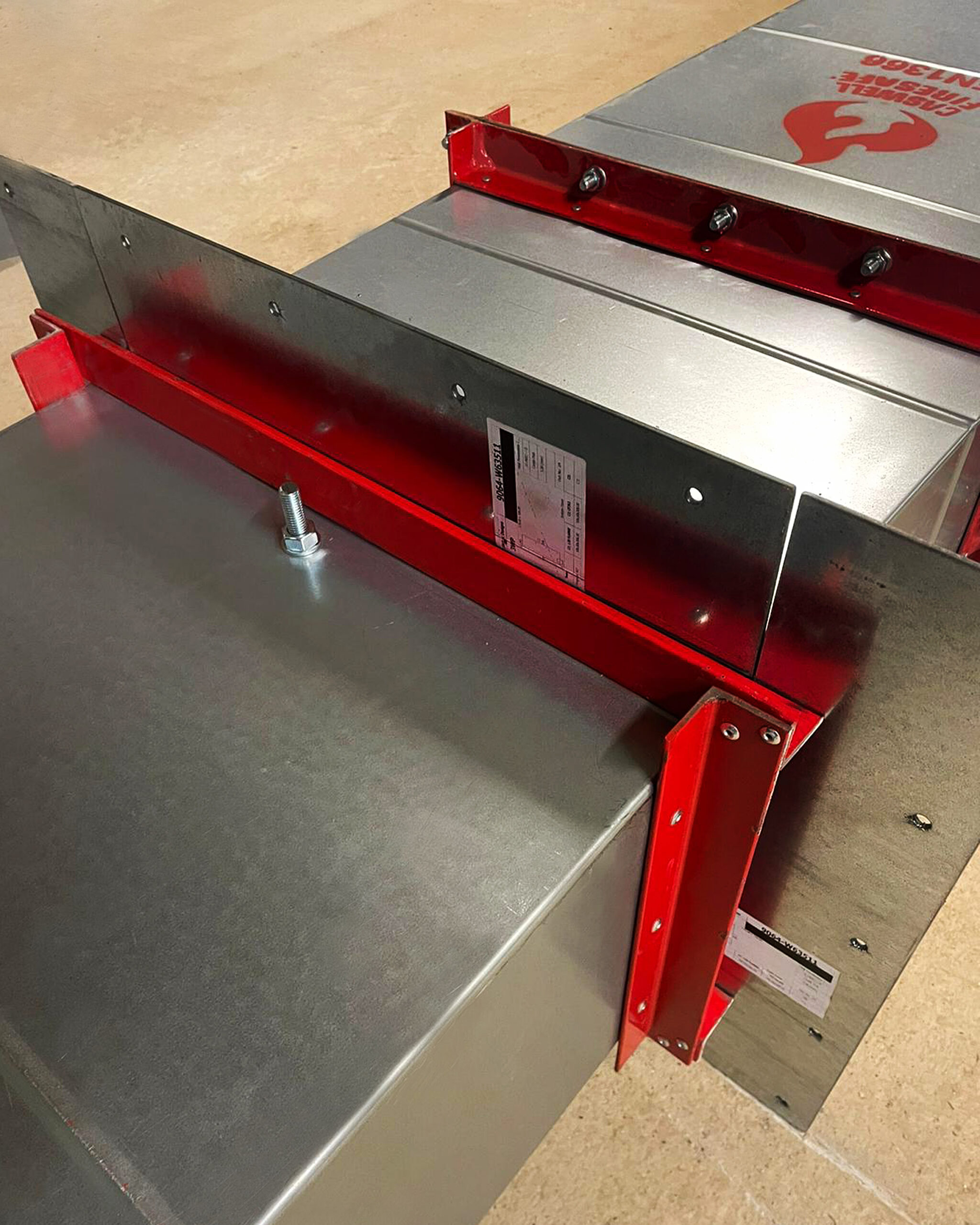
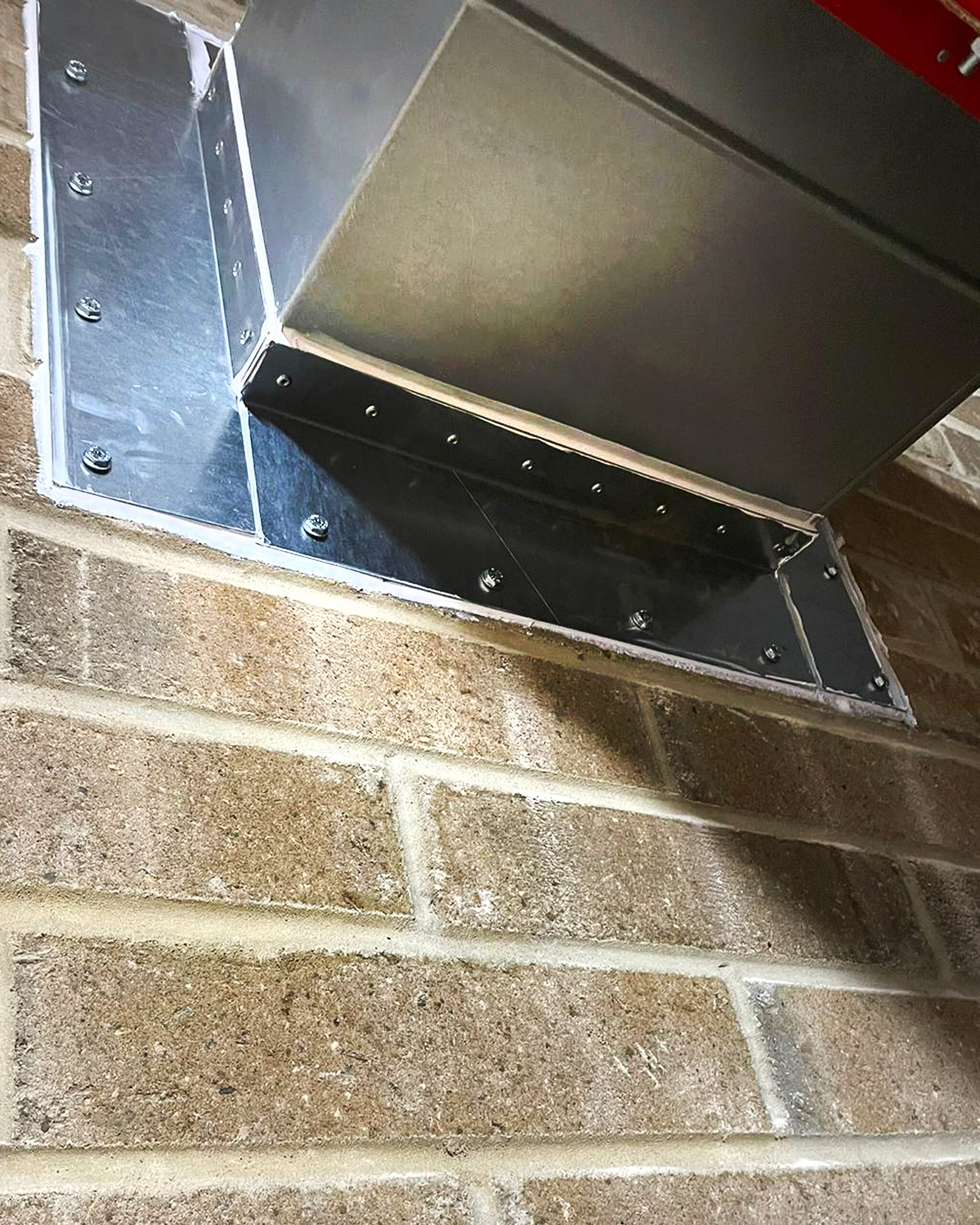
This regime will also provide a record of any penetrations that fall outside the fire duct manufacturer’s scope and into that of a fire stopping specialist. If required, corrective action can be issued to the installers and this would form part of the ‘Golden Thread’ of information for the Certification.
Inspections of each penetration would include as a minimum:
Photographic evidence – from both sides of the opening – at the following stages of the installation:
- Opening formed – No ductwork installed
- Ductwork installed through the opening (prior to any insulation being fitted, if applicable)
- Ductwork and insulation installed up to or through the opening (as applicable) prior to any collars being installed
- Completed installation including collars, sealant, pattresses and other ancillary products
The record should include the following details for each penetration:
- Unique ID for the penetration
- Drawing number or specific location of any penetration (floor, room etc.)
- The system specification / fire performance i.e. EI120 (Integrity & Insulation for 2 hours)
- Manufacturers penetration detail / reference, ‘as tested’
- Duct size
- Opening size in Separating Element
- Construction of Separating Element (i.e. Flexible Partition classified for 2 Hours)
- Annular space i.e. the distance from duct to inside face of formed opening
- ‘As tested’ arrangement (Yes / No)
- Photo ID’s as detailed above
- Corrective Action issued date and reference
- Corrective Action completion date / sign-off date
- Reference to any correspondence relating to non-compliant openings
Penetrations that are not correctly fire stopped will increase the risk of failure of the compartmentation. This puts lives in danger and increases the potential damage sustained by the building and its contents.
Fire stopping methods for pipe and cable services penetrations have existed for a long time. Fire resisting ducts are however inherently different in that they transmit heat and are also prone to increased movement, which can render ‘traditional’ methods of fire stopping unsuitable.
In summary
A change in culture is being witnessed but the industry needs assistance in the earliest stages of design to facilitate the move away from improvised designs towards fully-tested details, as stipulated in BS9999.