Malcolm Moss, ADCAS President
Association of Ductwork Contractors and Allied Services (ADCAS)
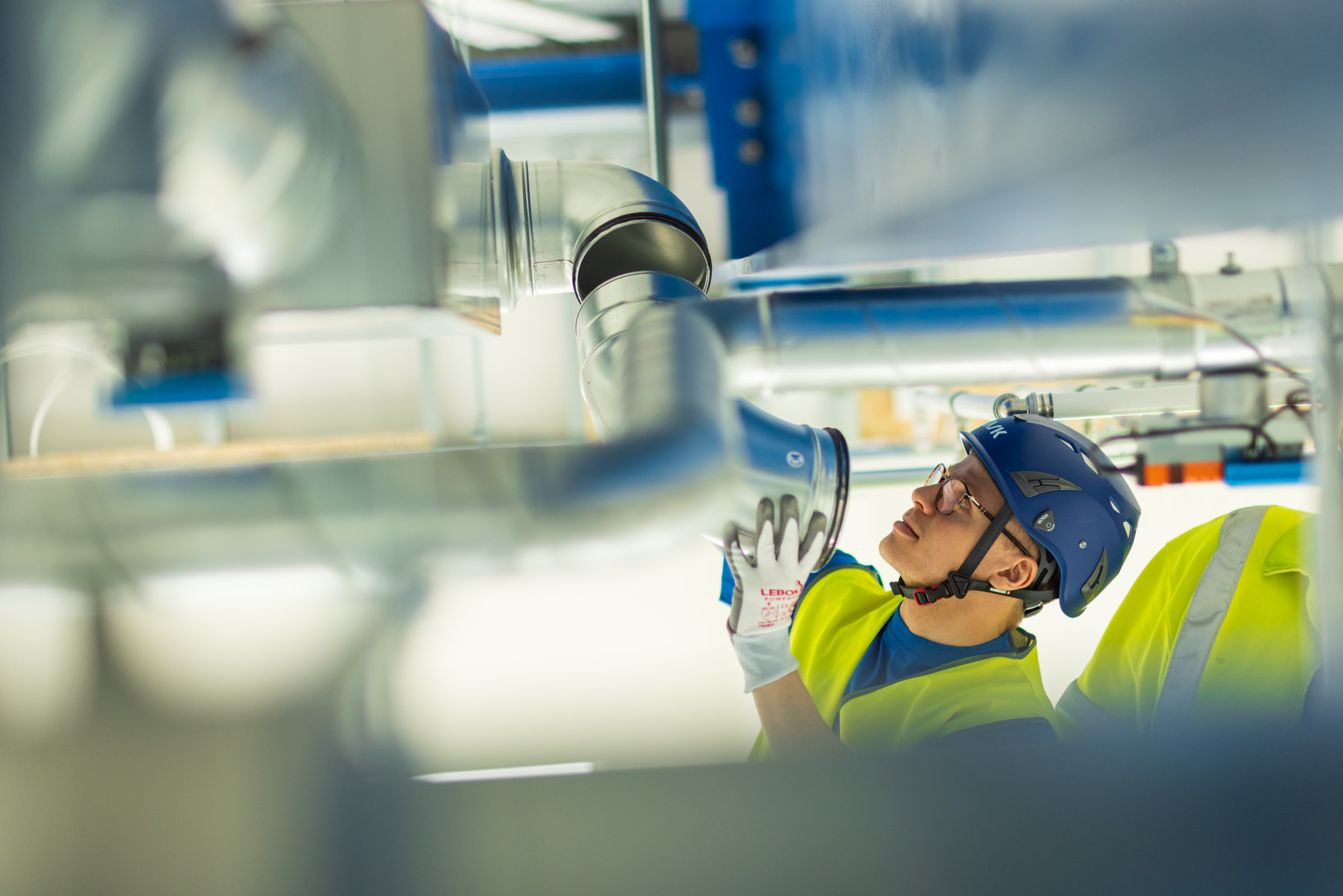
Setting high standards in ductwork
Malcolm Moss, President of the Association of Ductwork Contractors and Allied Services (ADCAS), looks at how to ensure competency through a combination of compliance to key specifications and the prioritising of training and professional development.
The ductwork industry plays a key role in ensuring that buildings meet required air quality and ventilation standards. Like many industries operating in the building services sector, is currently examining its approach to maintaining high standards and suitable levels of competency.
The industry is involved in a diverse range of sectors, including commercial buildings, residential developments, industrial facilities, and healthcare environments – each with unique requirements for air quality and ventilation. Though the setting may differ, in most indoor environments, ductwork is primarily used for the following purposes:
- Air distribution – transporting heated or cooled air from HVAC systems to different areas of a building.
- Ventilation – facilitating the exchange of indoor and outdoor air, helping to maintain indoor air quality by removing stale air and bringing in fresh air.
- Exhaust – in kitchens, laboratories, and industrial settings, ductwork is often used to remove smoke, odours, and harmful fumes, ensuring a safe and healthy environment.
- Dust and pollutant control – part of systems that help filter out dust, allergens, and other pollutants, contributing to better air quality.
Badly installed ductwork can result in poor airflow, increased energy costs, poor indoor air quality, reduced levels of comfort, noise issues, higher maintenance costs and non-compliance with regulations.
The UK has strict building regulations and standards that govern ductwork design and installation, ensuring safety, efficiency, and indoor air quality.
The latest edition of the DW/144 specification provides a foundation upon which industry standards can be built, but ongoing training is crucial to ensure these standards are met in practice.
Cornerstone of competence
The DW/144 specification remains the definitive standard for ductwork manufacture and installation in the UK. The latest edition, which reflects updates in technology, materials, and industry practices, sets out rigorous guidelines for the production, installation, and testing of ductwork.
Leakage from ductwork can have a significant impact upon overall building efficiency, which is why sheet metal ductwork leakage testing is so important and should be carried out in accordance with procedures set out in DW/144. Compliance with DW/144 ensures that ductwork systems are efficient, durable, and capable of meeting the environmental demands placed upon them.
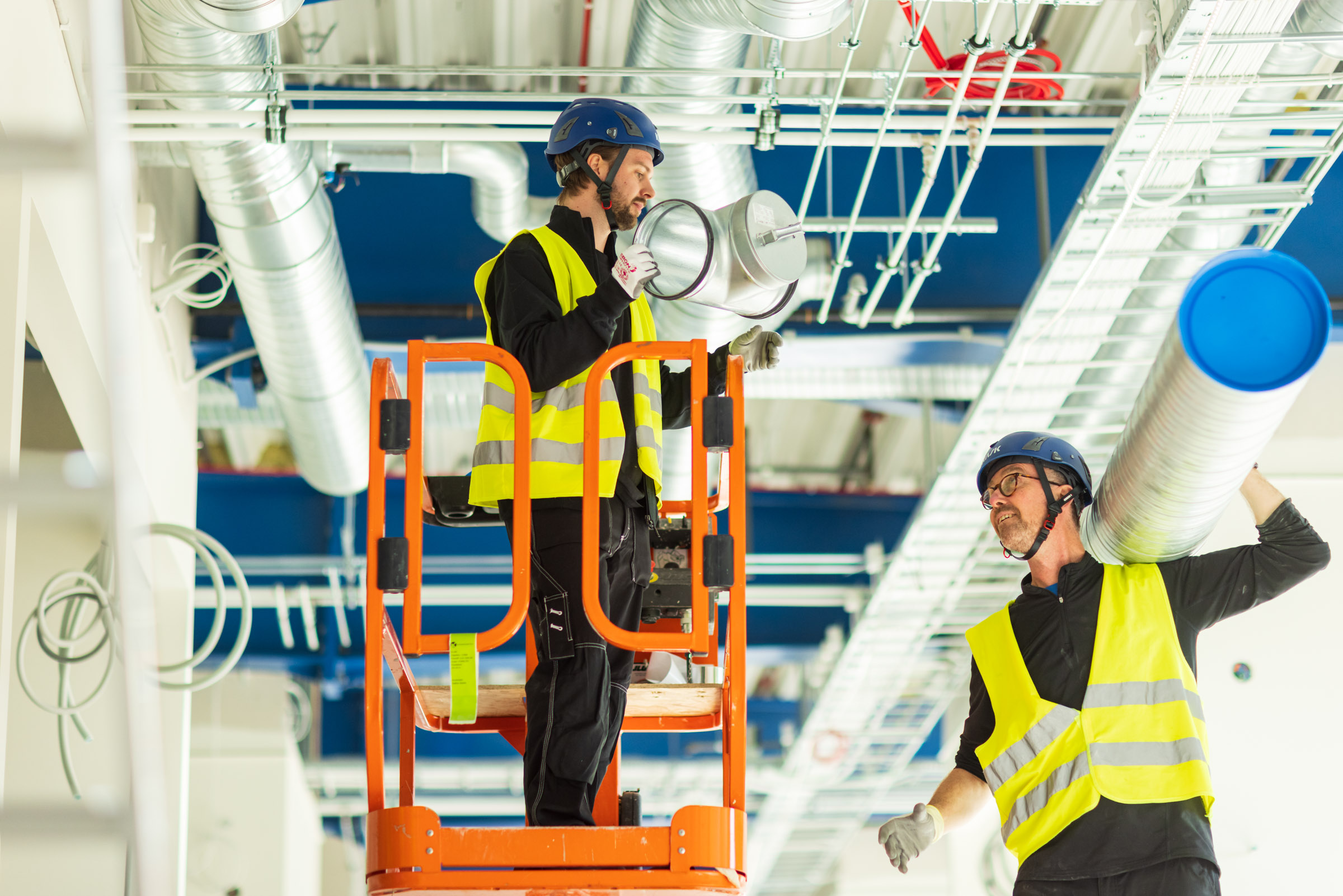
One of the primary functions of DW/144 is to standardise the quality of ductwork across projects, ensuring that installations are consistent and reliable. The specification covers a range of topics, including materials, construction methods, jointing techniques, and testing procedures. Adherence to these standards is critical for ensuring the performance and safety of ductwork systems, especially in environments where air quality is paramount, such as hospitals, laboratories, and office buildings.
The specification highlights the technical information to be provided by system designers to ductwork contractors and looks in detail at rectangular, circular, and flat oval ductwork. It contains updated information on hangers and supports, smoke and fire dampers, external ductwork, internal duct linings, thermal insulation, air terminal units and more, using tables of reference for additional clarity.
In addition to DW/144, there are several key pieces of legislation that impact the ductwork industry. The Construction (Design and Management) Regulations 2015 (CDM 2015) place significant responsibility on contractors to ensure that health and safety are prioritised throughout the lifecycle of a construction project. This includes ensuring that ductwork installations are carried out by competent professionals who are aware of the risks associated with their work. Similarly, the Health and Safety at Work Act 1974 imposes a duty on employers to provide adequate training and supervision to ensure the safety of their employees.
Other relevant standards include BS EN 1507 for sheet metal ductwork (characteristics and test methods to determine strength and air leakage of rectangular ductwork) and BS EN 12237 for rigid circular ductwork (requirements, terms and definitions, and test methods to determine the strength and air leakage of circular ductwork). These standards complement DW/144 by providing specific guidelines on the design and performance requirements for different types of ductwork systems. Compliance with these standards is essential for ensuring that ductwork installations meet the necessary performance criteria and are safe for use in a variety of environments.
Though these specifications and standards play a vital role in ensuring best practice, high levels of competency amongst installers in equally important and shouldn’t be overlooked.
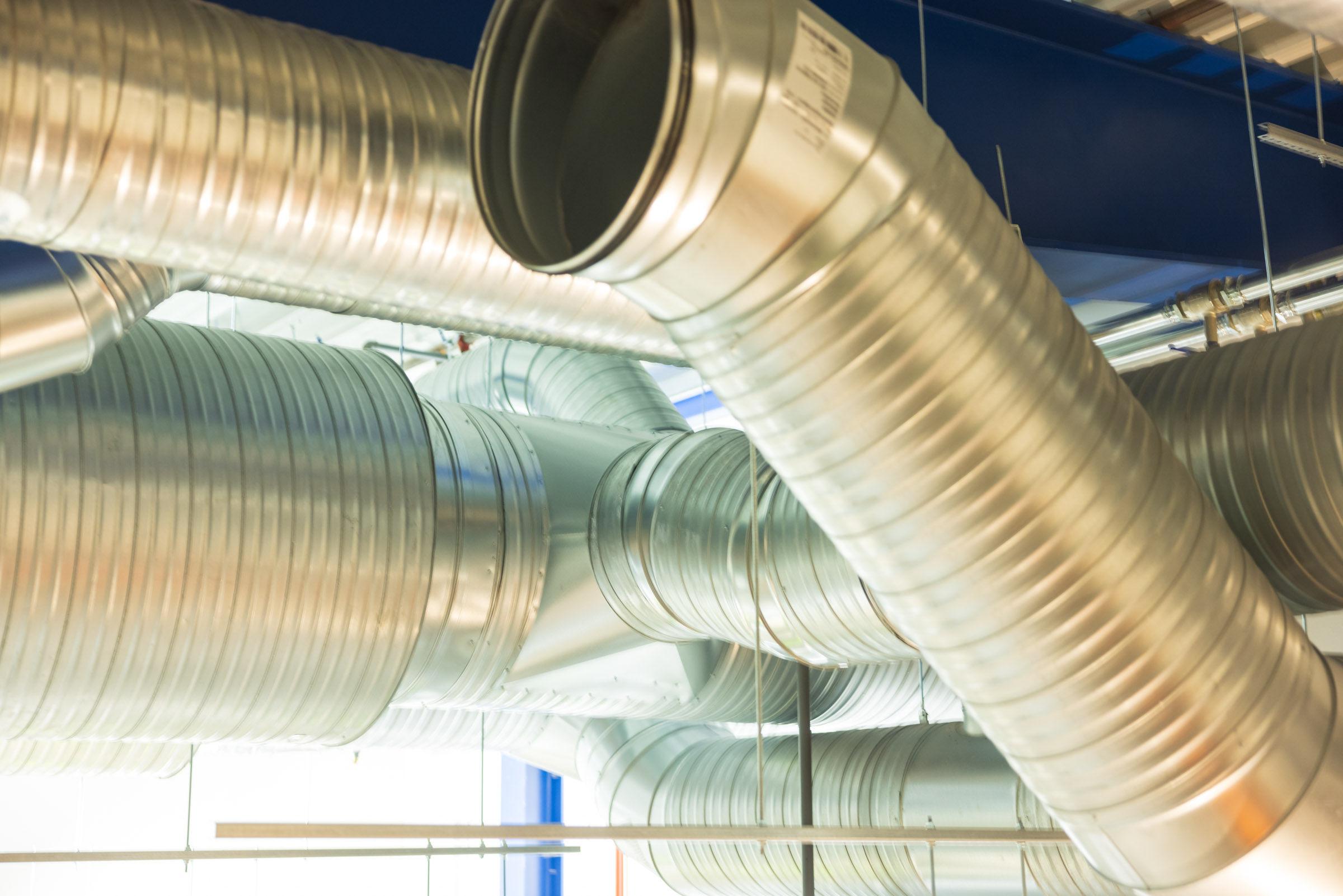
Building a competent workforce
Employers play a crucial role in improving competency levels within the ductwork industry. By prioritising training and professional development, they can ensure that their workforce is equipped with the necessary skills and knowledge to carry out their work to the highest standards.
As a nationally recognised qualification, an SVQ in Ductwork Installation is often the favoured route towards demonstrating competency. The Level 2 SVQ in Ductwork Installation focuses on the foundational skills required for the installation and maintenance of ductwork systems. It is suitable for those new to the field or those working under supervision.
The qualification covers various aspects of ductwork installation, including:
- Understanding and applying health and safety regulations
- Interpreting technical drawings and specifications
- Cutting, shaping and assembling ductwork components
- Installing ductwork systems according to standards and best practices
- Testing and commissioning installed systems
- Troubleshooting and rectifying issues with ductwork installations
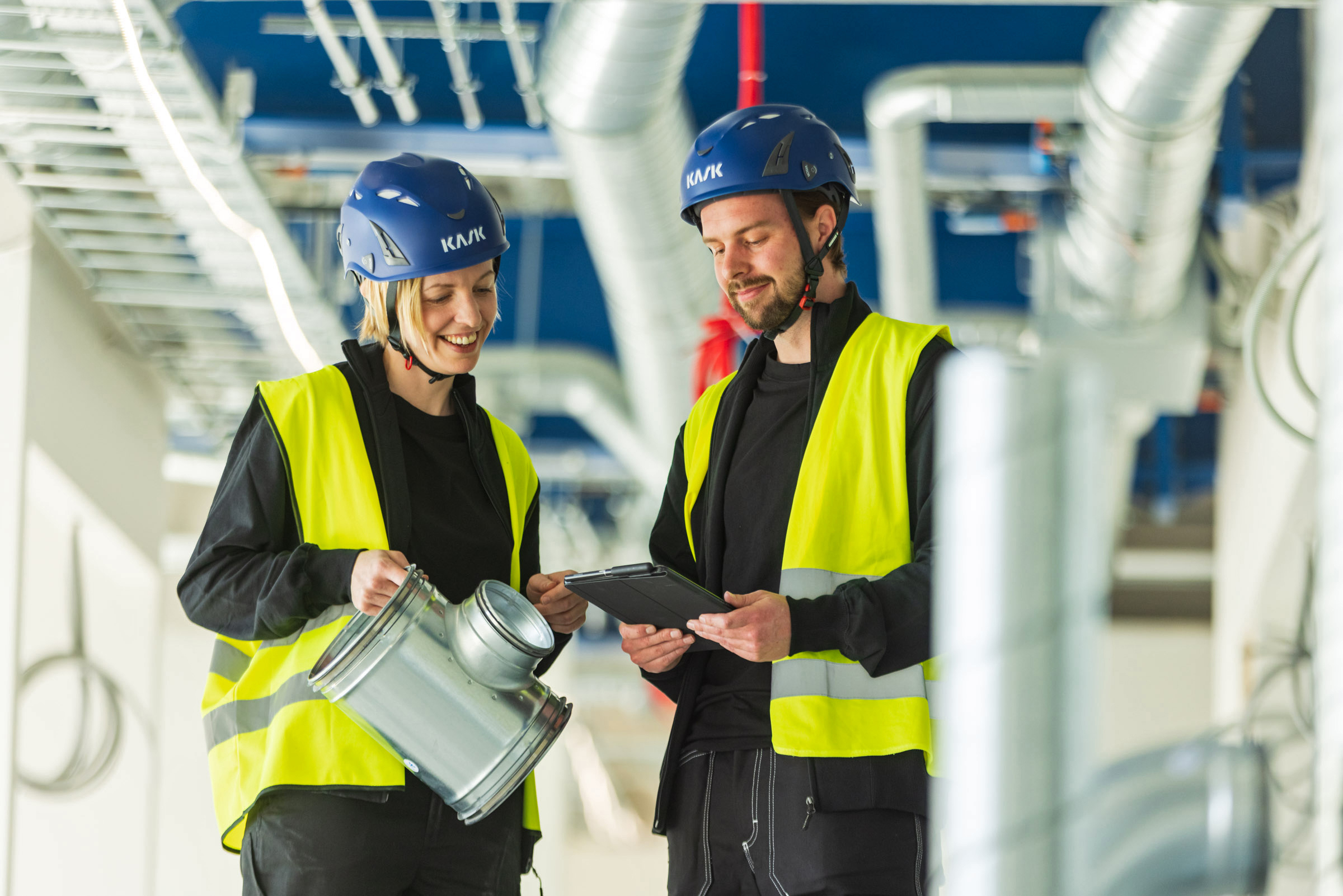
SVQs are assessed through a combination of practical observation, work-based evidence (e.g., reports, logbooks), and sometimes written or oral questioning. Since SVQs are work-based, candidates usually need to be employed or have a placement in a relevant role to complete the qualification. This allows them to demonstrate their skills and knowledge in a practical setting.
With time now about to be called on CSCS cards obtained through industry accreditation, experienced workers will shortly need to enrol on an SVQ relevant to their skillset and pass an experienced worker assessment within 18 months of enrolment.
Previously, Industry Accreditation (IA) allowed individuals to obtain CSCS-backed cards based on their experience without the need for a qualification. However, these will be phased out and all current cardholders will require relevant approved qualifications to access a site.
These changes are being introduced as a response to the Grenfell Tower tragedy and the subsequent recommendations made by Dame Judith Hackitt. The Construction Leadership Council (CLC) then issued card scheme recommendations that are being adopted throughout the industry.
As things currently stand, the SVQ in Ductwork Installation is the sole route to proving competency in the ductwork industry, though ADCAS is currently working with other industry stakeholders to explore new training options to ensure that ductwork operatives are able to prove competency in a satisfactory manner – both now and over the long-term.
Commitment to excellence
Industry bodies such as ADCAS play a central role in promoting competency within the ductwork industry. By providing guidance, setting standards, and exploring new training opportunities, ADCAS is ensuring that the industry continues to improve and evolve.
The DW/144 specification provides a strong foundation but should be supported by ongoing training and professional development. By investing in the workforce and promoting a culture of continuous learning, the ductwork industry can meet the challenges associated with modern construction and deliver high-quality, safe, and efficient ductwork systems.