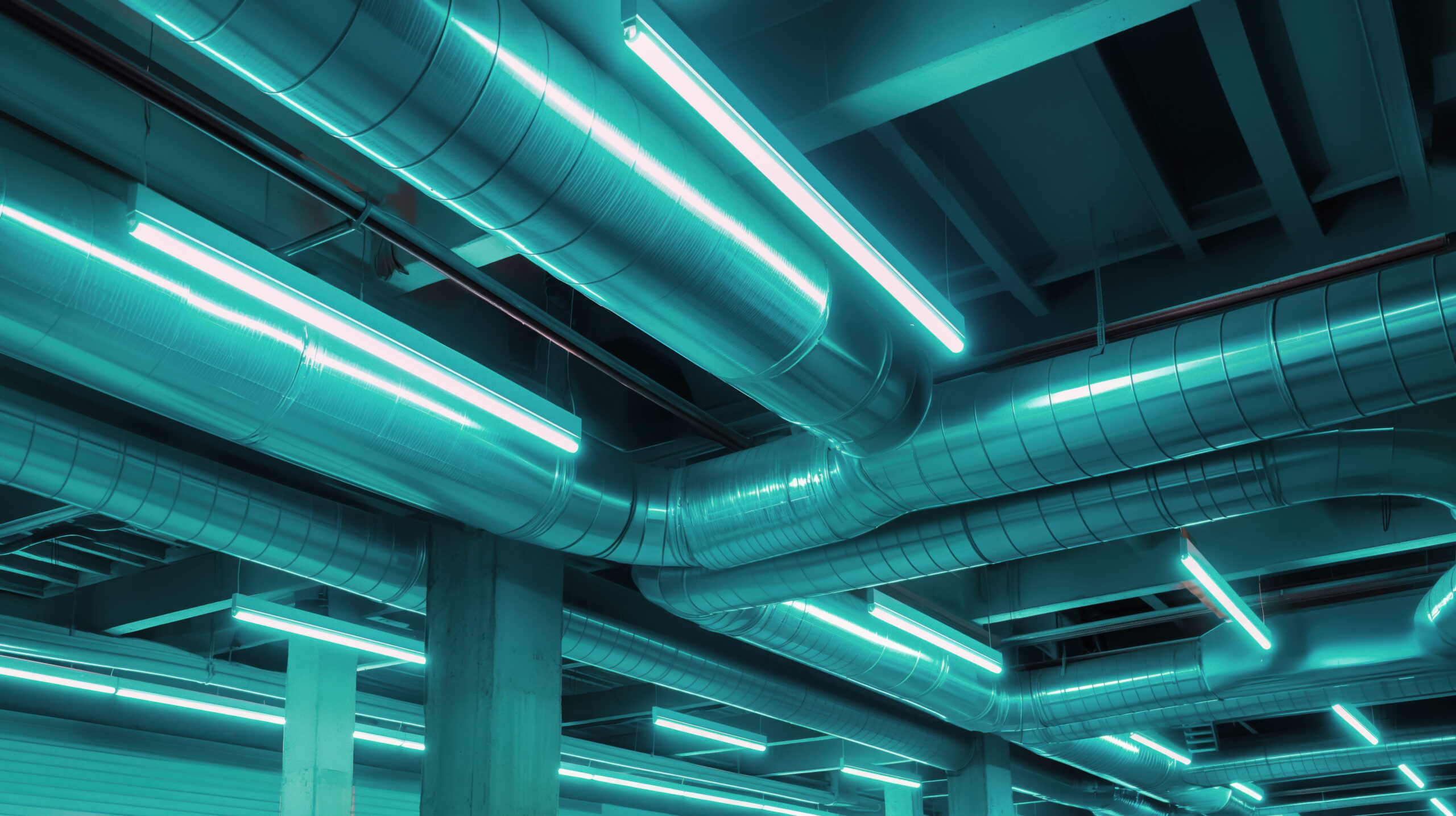
Ventilation hygiene in the built environment
The inspection, cleaning, and maintenance of ductwork is a vitally important part of building facility requirements.
System cleanliness is critical, and it is imperative that all parts of a ventilation system are considered as part of a testing, inspection and maintenance regime.
The purpose of ventilation hygiene is the betterment of the environment and to reduce the risk of fire spreading within any building.
Building owners have a responsibility to the occupants of the building and should ensure that a competent accredited company conducts regular inspection, cleaning, and maintenance of ductwork under HSE 1992 Rev 2013.
Indoor air quality (IAQ) is often overlooked as an issue for public health and many circumstances, from poor hygiene standards to poor maintenance or no maintenance, can lead to the presence of potentially harmful organisms and in some cases pathogen growth.
Lack of maintenance also increases the risk of the spread of fires and under Regulatory Reform (Fire Safety) Order 2005 it is the responsible persons duty to identify and control risks. Any ventilation system should be included in this assessment identifying risk, hazards and control measures to ensure protection and the prevention of fire risk.
Ventilation hygiene has been neglected for many years and the Covid pandemic highlighted our collective shortfalls. Proper maintenance is a key issue for people occupying buildings, particularly as we are now more conscious of the air we breathe, its contaminants and the time we all spend indoors.
Maintaining and cleaning ventilation systems is a legal requirement and should no longer be overlooked by facilities managers and persons responsible for overall building safety.
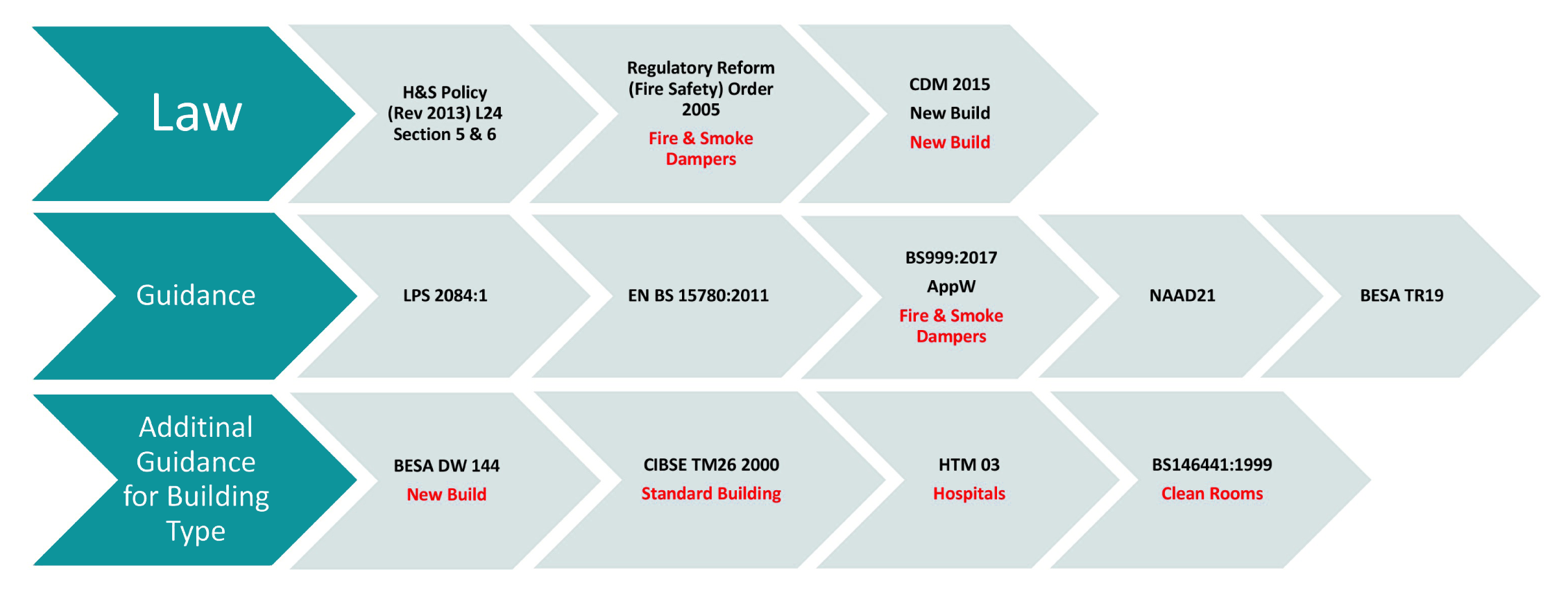
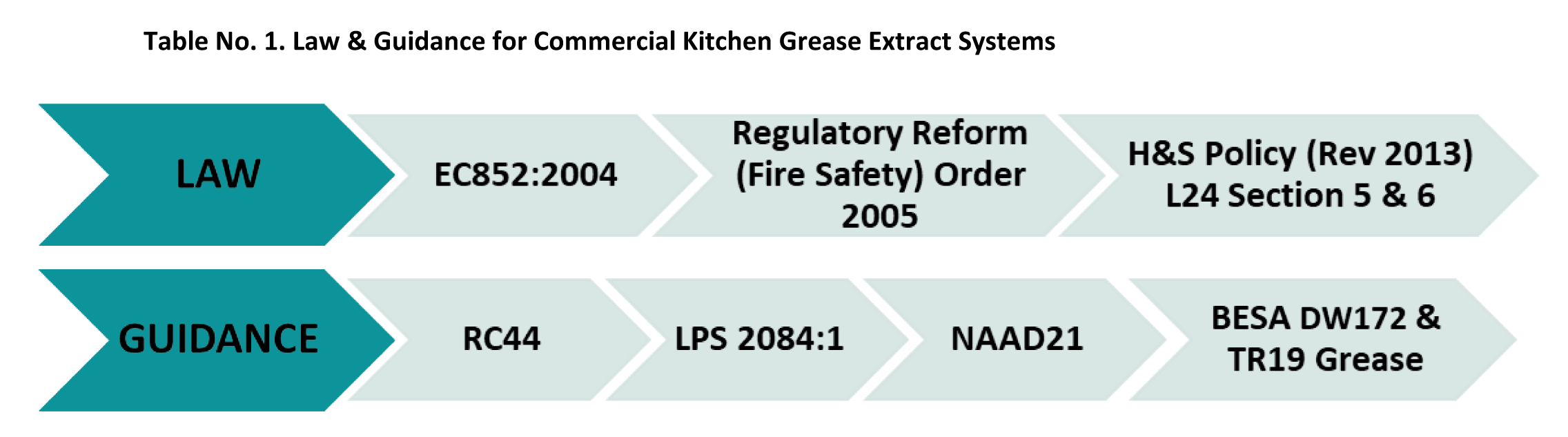
Building classifications, inspection frequencies and limits
Inspection frequencies are clearly defined in BS:15780, NAAD-21 and TR:19 and state that:
“All ventilation systems should be subject to, at least, a simple visual inspection annually ventilation systems serving critical care areas should be inspected quarterly and their performance measured and verified annually. The quarterly inspection should be a simple visual check; the annual verification will be a more detailed inspection of the system together with the measurement of its actual performance. “
Ventilation hygiene has building classifications that clearly identify certain office spaces as a ‘High Quality’ area as shown in the table below:
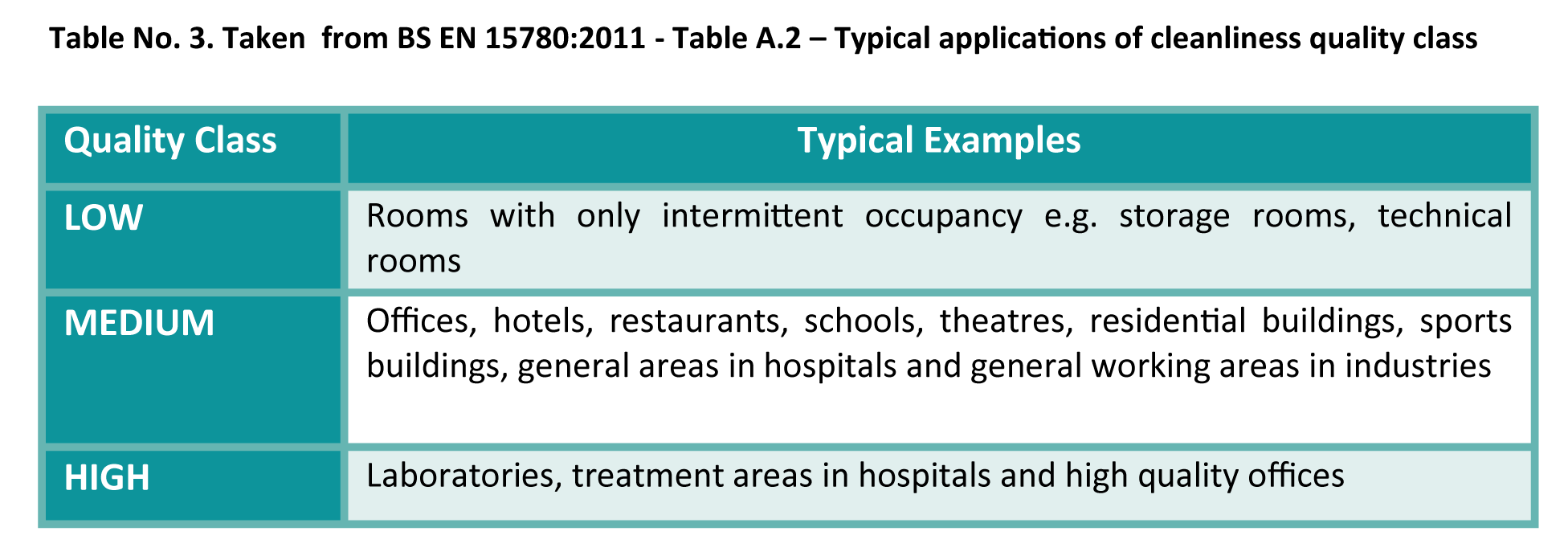
Highlighted in BS EN 15780:2011, there is a recognised regime for inspection and maintenance in the built environment and it is clearly defined within NAAD-21, as outlined in the table below:
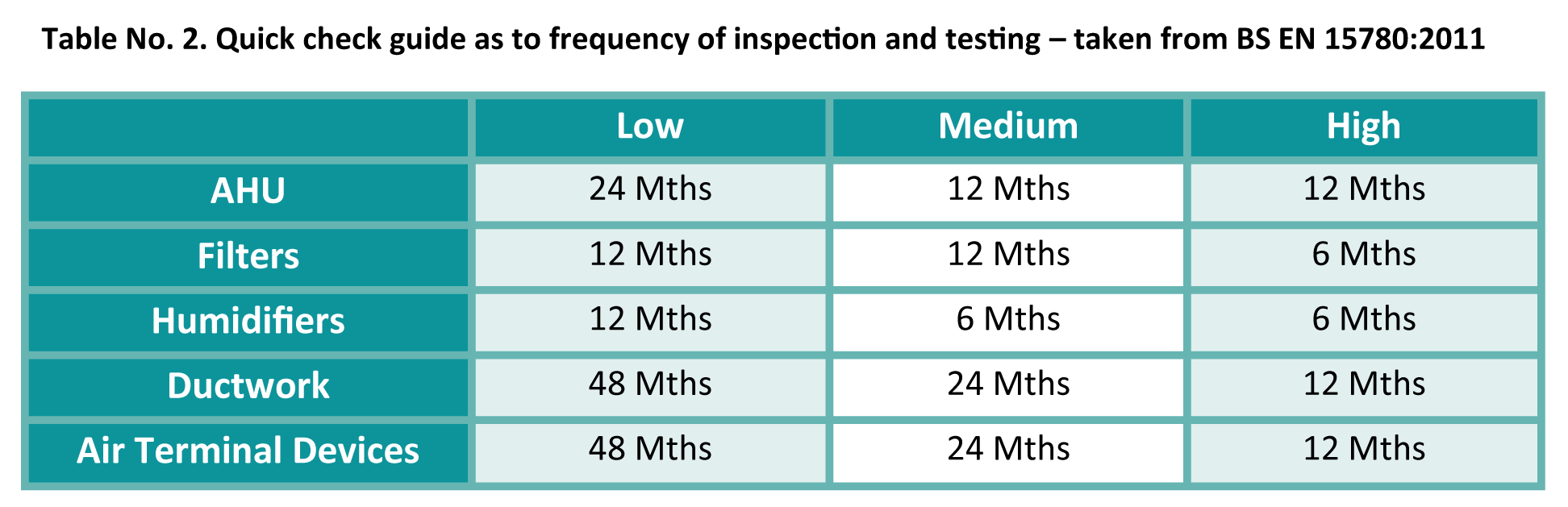
Ventilation hygiene requirements in these areas are clearly defined and show what constitutes a compliant acceptable level of cleanliness within systems.
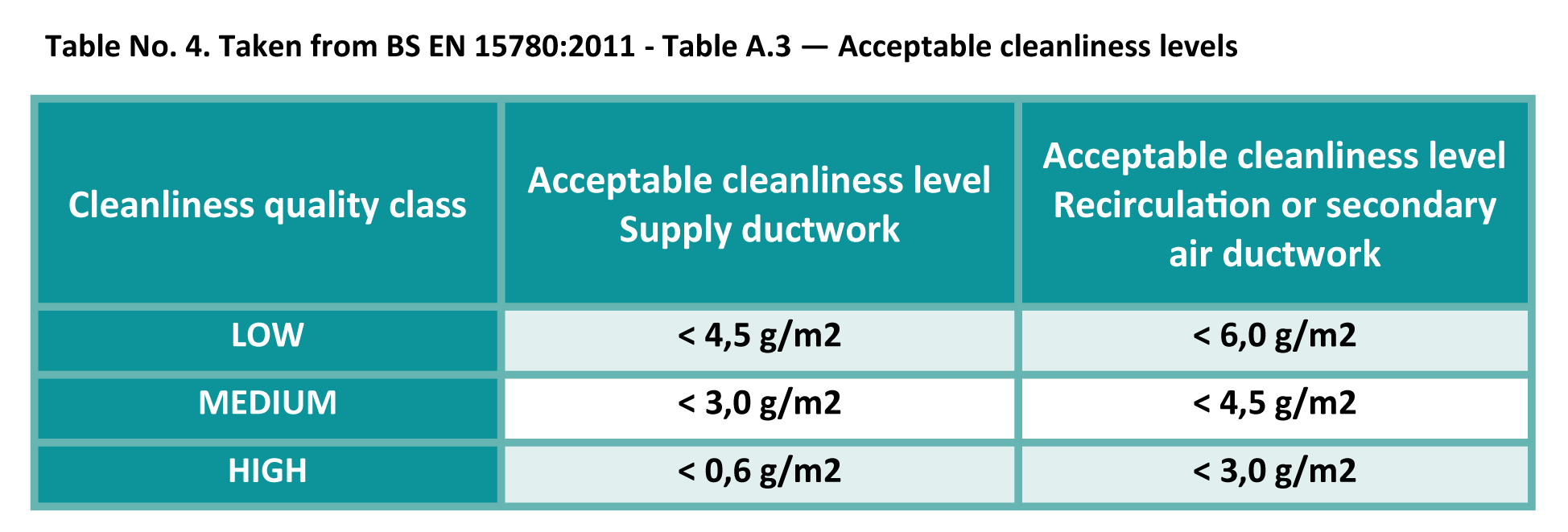
Even new systems have acceptable cleanliness levels, as shown in the table below:
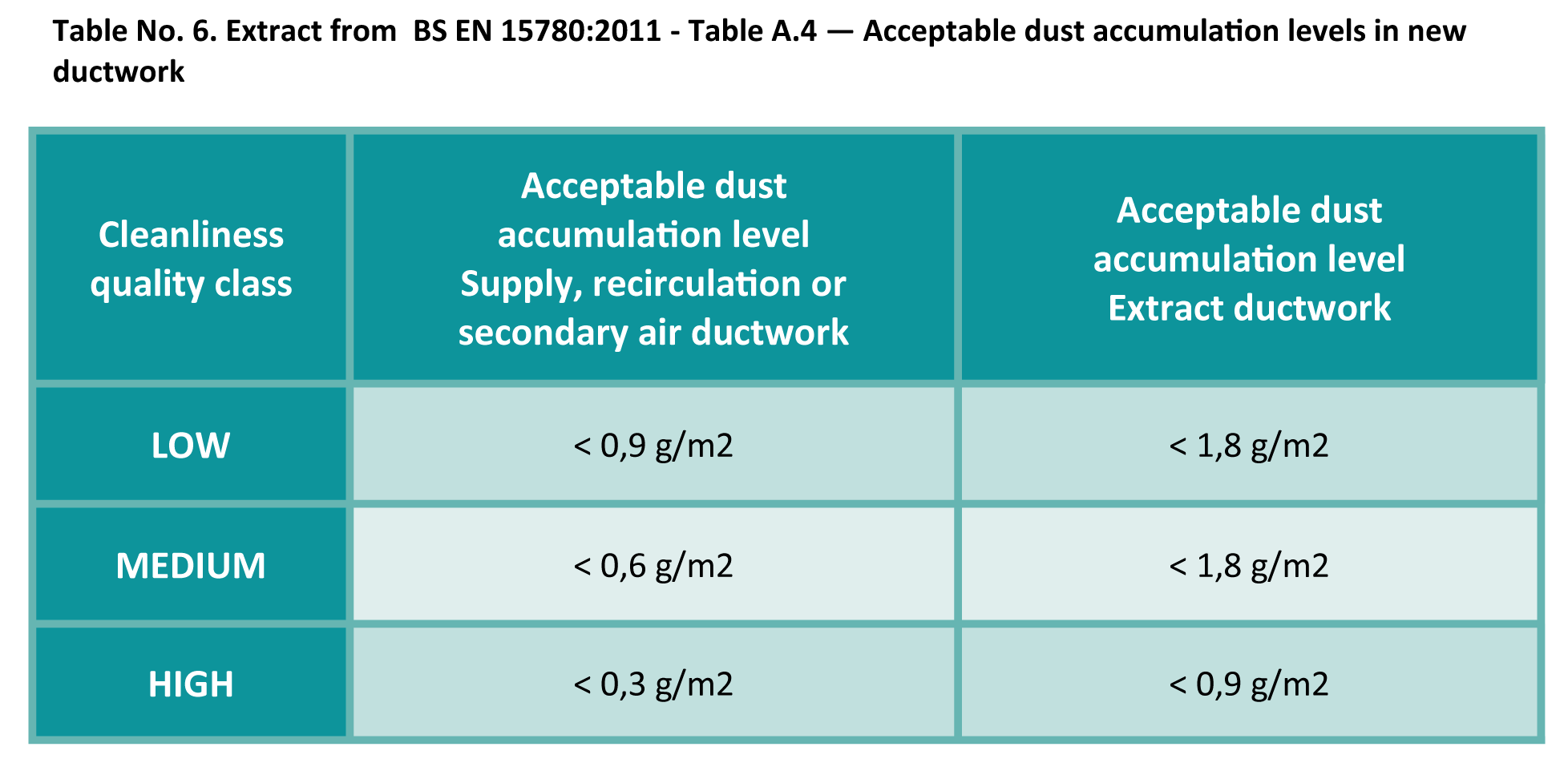
Who should be conducting the testing, inspection and cleaning?
NAADUK has been working with others within the sector to improve the standards of maintenance which resulted in the publication of NAAD21.
With the collaboration of training instructors, auditors and assessors, a full programme has been developed to create a certification to a SCQF Level 6 standard. It covers the practices and procedures of the BSEHV11, the National Occupational Standard for cleaning industrial and commercial ventilation systems. This qualification should be considered the minimum standard for ventilation hygiene technicians.
All testing and cleaning in the built environment should be conducted by competent qualified persons and the company that is completing the works should have third party accreditation such as the LPS:2084 scheme.
Section 10 of NAAD-21 highlights this clearly.
How should the testing be completed?
There are several recognised testing methods when it comes to ventilation hygiene levels these are predominantly split into two categories:
• Dust Contamination
• Microbiological
The NAADUK tests for these are as follows:
• Vacuum testing (with the adapter)
• Contact slides
• Agar plates
Other approaches include Deposit Thickness Tests and the Wiping Method. However, NAADUK does not recommend these methods, as they are typically not sensitive enough to be accurate on post-clean.
NAADUK recommends the Vacuum Test (VT) test to be used for dust sampling using pre-weighed filter cartridges, pre-barcoded to prevent mistakes or incorrectly-attributed figures. In addition, we suggest working with an independent laboratory to UKAS standards, which provides full certification. All microbiological samples should also be tested by an independent laboratory to UKAS standards, which provides full certification.
The parameters for microbiological contamination can be found in CIBSE TM26 Table 3 – Classification of surface sampling microbial limits.
All testing and inspections should have the information recorded in a clear, concise, photographic report, incorporating laboratory analysis certificates and advisory notifications.
What should happen when a sample fails?
Whenever a sample location is above recommended parameters, this does not mean that the whole system requires cleaning as highlighted in CIBSE TM26 10.2.2 for microbiological sampling.
With dust contamination, we must look at the system criteria with a qualified competent person making a scientific evidence-based assessment and recommendation for either localised or full system cleaning.
How should a clean be conducted?
All cleaning in ductwork should be undertaken in the direction of air flow, contractors should isolate zones where possible through the open/shut operation of VCD. On all dry-cleaning methods, make sure a suitable (negative air) air mover machine is in place with suitable filtration appropriate to the standard of cleaning.
Wet cleaning methods should be avoided, if possible, as they can lead to an increase of microorganisms if incorrectly applied. If we cleaning is required, the system must be thoroughly dried before commissioning.
NAAD-21 Table 9 Below explains cleaning methods:
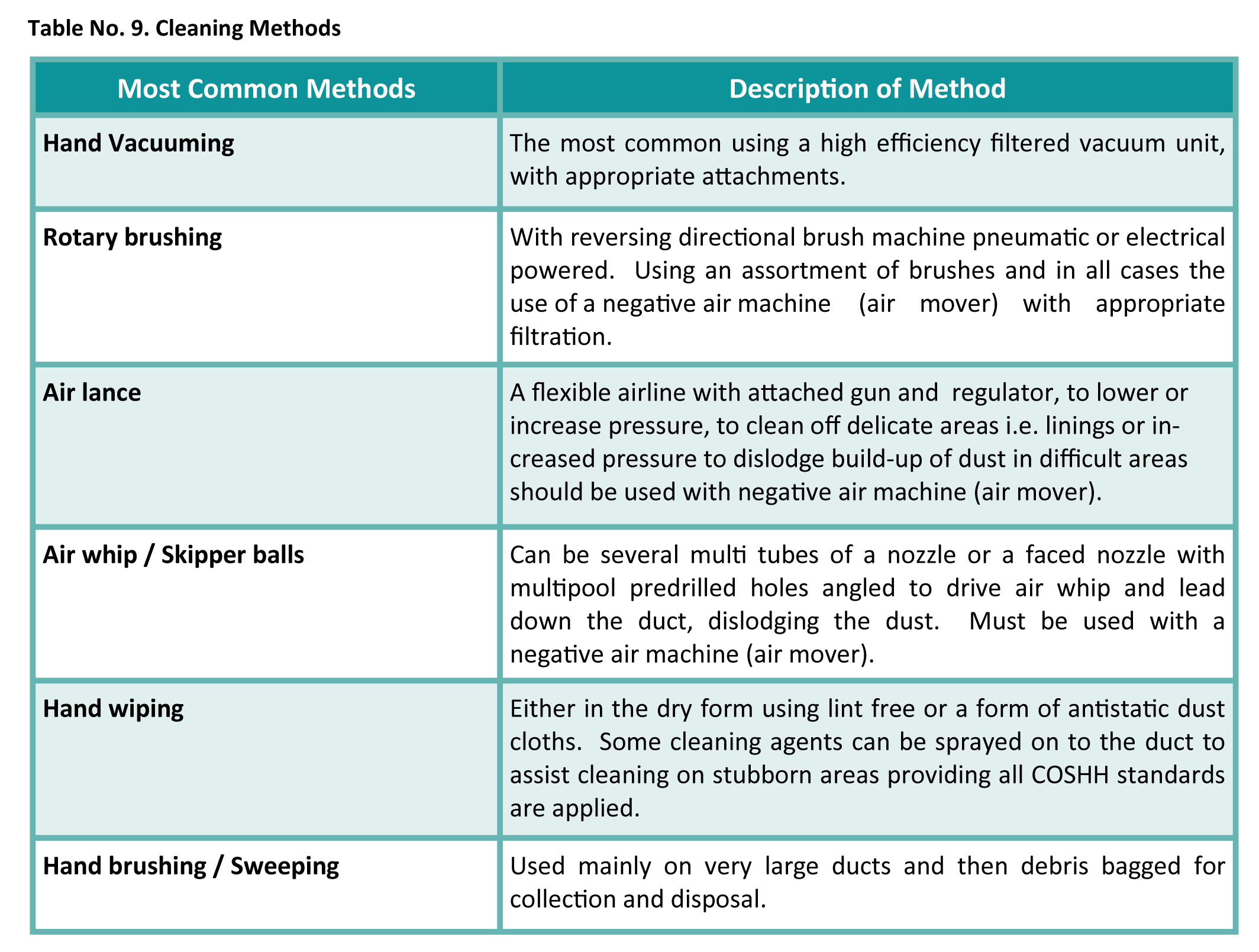
All cleaning reports should contain post-cleaning testing that was the same UKAS method as highlighted in the pre-clean. All pre- and post-clean information should be recorded in a clear, concise, photographic reports, incorporating laboratory analysis certificates and any agreed out of scope areas.
Ventilation and health
Ventilation maintenance is critical for the health and wellbeing of all persons within the built environment. With elevated awareness and the necessity for compliance and reduction of risk, Ventilation Hygiene Assessments must form part of a competent compliant PPM regime using only proven competent technicians.
If surveys and cleans are conducted by 3rd party accredited companies, with NVQ/SVQ qualified technicians, UKAS laboratories and detailed photographic evidence-based reporting. This will push higher standards, cleaner environments and better health and wellbeing within all settings.
* NAAD-21 Guidance Document for Ventilation Hygiene Part 1 GREASE (Kitchen Extract) – Legal Standards and Guidance applicable to the risk management of the fire and grease levels within commercial kitchen extract systems to EC852:2004 and Part 2 AIR (Indoor Air Quality) – Regulation guidance standards for Indoor Air Quality in occupied zones. Printed January 2022 and launched Feb 2022 authored by members of NAADUK (National Association of Air Specialists UK). For further information, advice or free copy of NAAD-21 hard copy or pdf, please visit www.naaduk.co.uk