Matthew Blackmore, Head of Business Development at Armstrong Fluid Technology.
Armstrong Fluid Technology
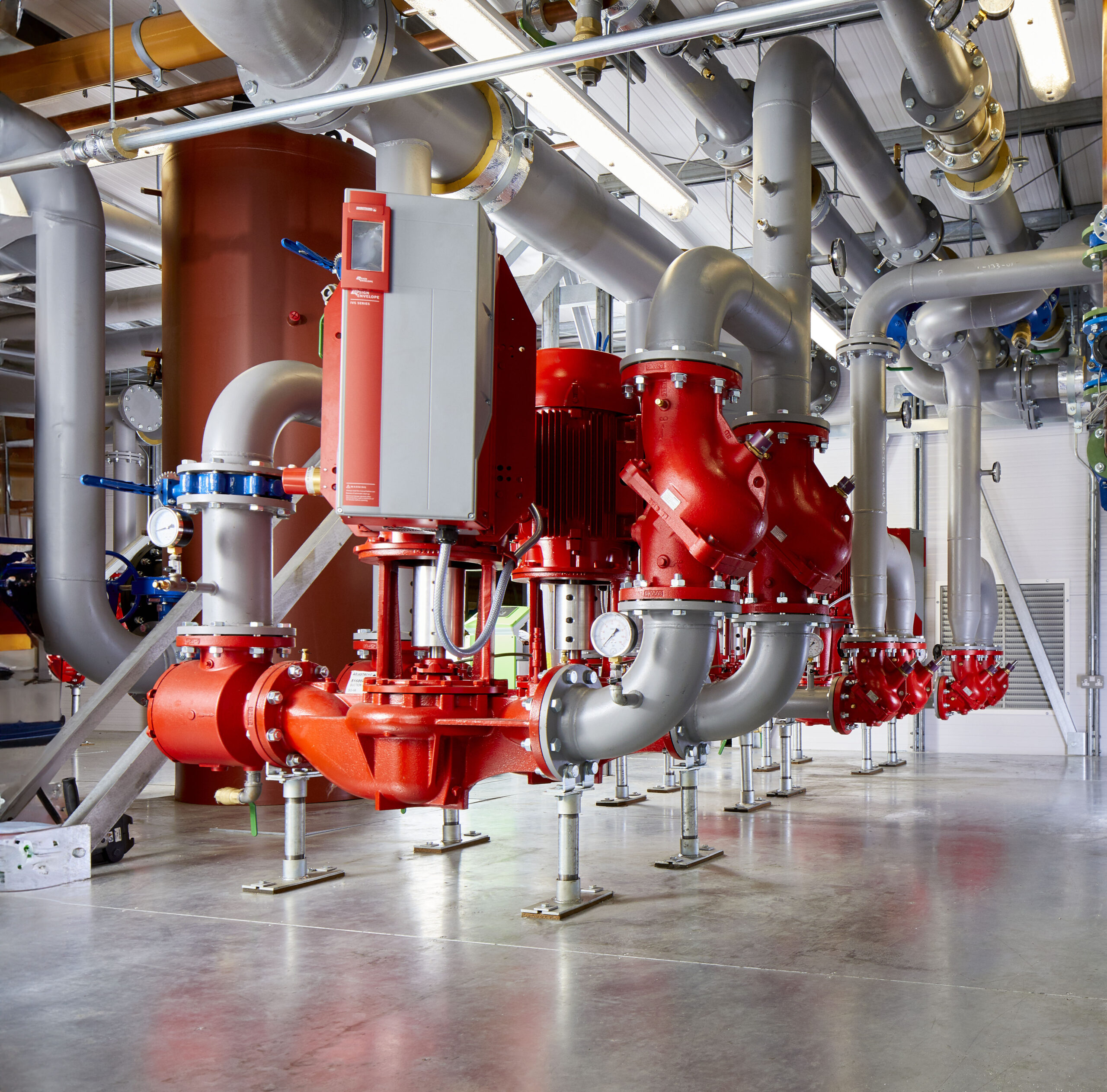
Energy upgrades: harness the power of pump connectivity
Matthew Blackmore, Head of Business Development at Armstrong Fluid Technology explains why it’s important not to overlook the possibilities for carbon and cost savings when updating your pumps.
In many ways, the leaps forward in pump technology over the past decade rival or surpass the gains made from the industry’s move from fixed speed to variable speed pumps. Connectivity, smart commissioning and AI-powered control methodologies have transformed the pump into an intelligent and communicative brain, constantly reacting to variables within the system itself.
As well as using machine learning to operate in the most efficient way possible, modern pumps can predict maintenance problems, proactively warning custodians of problems which may occur in the future, resulting in savings in both carbon and maintenance costs.
So what opportunities are being overlooked?
The technology available for today’s generation of pumps can:
- Prove energy efficiency potential and secure cost savings for the upgrade, even while the project is still in the design phase
- Prevent energy efficiency levels from deteriorating over time
- Reduce embodied carbon of the installation
Intelligent system design
Today’s intelligent HVAC pumps have a crucial role to play during the design phase for energy upgrade projects, as well as after implementation. These latest generation pump models can track and collect data with greater accuracy than traditional flow meters.
Engineers are already becoming accustomed to the embedded software incorporated in these pumps, and many sites are now routinely harnessing the monitoring and reporting capabilities of the latest-generation pump models to optimise their performance after installation.
So why not harness the pump’s advanced monitoring and reporting capabilities to collect the data required for designing the new system, instead of using flow meters?
By approaching the energy upgrade in phases and installing the new pumps ahead of the rest of the project, the pumps themselves can supply the necessary data, with a high degree of detail and accuracy.
Most importantly, building owners and occupiers can start to save energy from day one, month one of the initial discussions. The building and load-specific information obtained via the pump software identifies opportunities for system optimisation with high cost/benefit ratios. This assists product selection and system design for the upgrade project, whilst actual, measurable energy savings are demonstrated in real time, throughout this process, to provide a more persuasive business case for stakeholders.
Breaking the project down into smaller sub-projects improves cash flow, and the business case begins to write itself. Depending on the system and load profiles, total energy savings of up to 40% are possible via this approach.
Another important development of recent years is digital twinning, which can now bring the power of AI to HVAC design. In the past there were various ways to calculate potential energy savings of different HVAC system designs. Traditionally, mechanical engineers/consultants and building owners have always had to base information on maximum calculations. What was needed was a more realistic and accurate method of calculation and verification.
Engineers often think that these technologies are way off in the future, but digital twinning is already delivering these benefits, and the tools are readily available and being used today in our projects.
With digital twinning, engineers can rapidly receive a quantified report on the impact of introducing heat pumps, or replacing a specific pump model, with actual calculations of the resulting savings in energy consumption, energy costs and carbon reductions provided by the technology in minutes. Using these insights the simulation also calculates the payback period and return on investment.
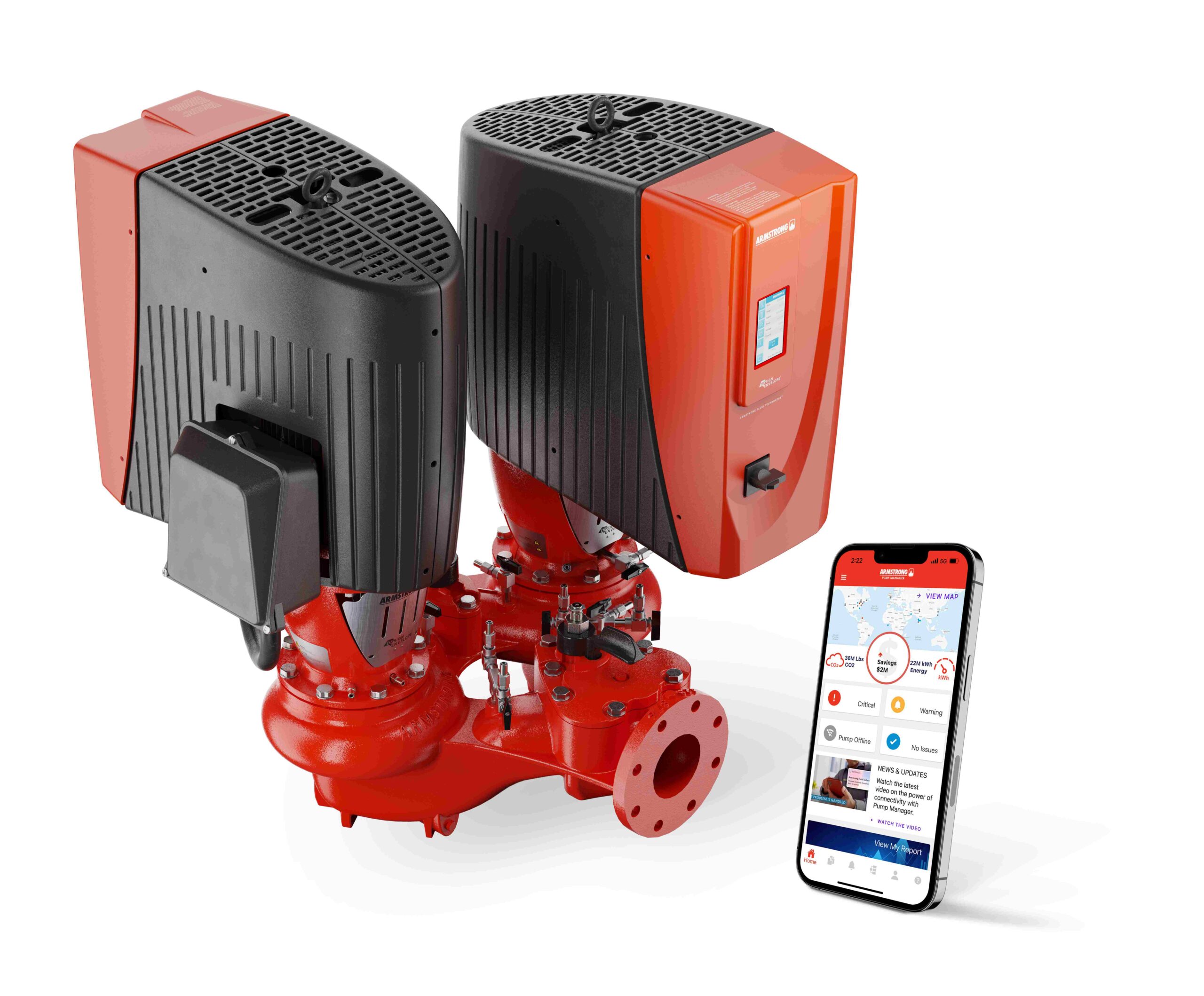
After installation of new or upgraded systems, the performance and resulting savings can be verified using the same digital twinning technology. Leveraging cloud computing makes it possible to carry out calculations that were never possible using traditional computer simulations. At last, important technical and financial decisions can be analysed comprehensively in advance and based on a firm scientific basis.
Maintaining energy efficiency – even at a distance
Today’s generation of pumps can also perform important diagnostic tasks, constantly recording and feeding back information to the facility/maintenance manager. With this the user is not only given the information needed to maintain efficiency of the system but is alerted if problems could be about to arise.
An active performance management service such as Armstrong’s Pump Manager, for example, provides the user with real time data from the system and each pump individually, and utilises machine learning to eliminate energy drift, providing up to 30% savings. Predictive diagnostic information is also available. The application uses the data it receives, directly from the pumps, to detect the future possibilities of problems such as bearing failures and cavitation, reducing and mitigating equipment failure and realising around 50% savings in maintenance costs.
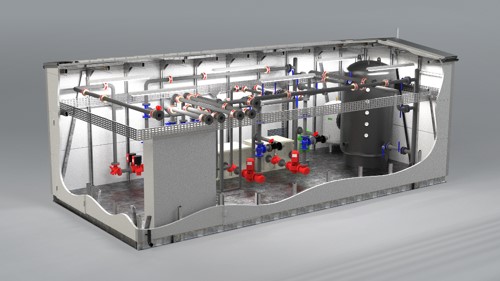
An important benefit of full pump connectivity, of course, is that the performance of heating and cooling systems in multiple locations can be analysed remotely. Local HVAC engineers in the areas where the pumps are situated can be given expert guidance from a central point, anywhere in the world.
With access to highly-detailed real-time data on performance of individual pumps, the specialist employed to oversee the performance of HVAC systems can manage any intervention at any site remotely and provide advice on any actions that need to be taken by local engineers. This provides an additional safeguard that comfort conditions will not be compromised for building occupants.
Reducing embodied carbon with parallel pumping
The practice of specifying full duty/standby pump installations is so widespread that it has not traditionally been questioned. On a day-to-day basis, one pump (sized for full duty) is operational while another of the same size is out of action, simply there to accommodate 100% redundancy in the event of routine maintenance or pump failure. This has a huge impact on cost and embodied carbon, which is becoming increasingly important as developers and designers strive to meet new targets and standards.
In installations such as hotels, offices and retail stores, or sites considered low risk (such as schools and apartment blocks) there are far more sustainable, efficient and cost-effective ways of safeguarding pump operation than having pumps standing idle ‘just in case’.
Adopting a parallel pumping strategy (specifying two smaller pumps, each sized for 50% of the design flow) in preference to a 100% standby approach, can reduce first installed and lifecycle costs, free up space in the plant room or energy centre, and potentially halve the embodied carbon for the installation. Pump solutions are available that incorporate two pumps into a single case. Embedded intelligence and connectivity allow for parallel pumping which delivers significant energy savings as well as reduced lifecycle costs.
And when you’re considering embodied carbon, don’t forget that the bodies of some brands of legacy pumps can be left in place, with just the controls and motor elements needing to be upgraded. This can save downtime and cost, minimise disruption, and have a major positive impact on embodied carbon performance.
In conclusion, it is time to look again at the technology resident in HVAC pumps, and the advances in connectivity that can improve effectiveness of design, long-term performance and environmental impact.