Martin Whiteley, Managing Director
Roperhurst
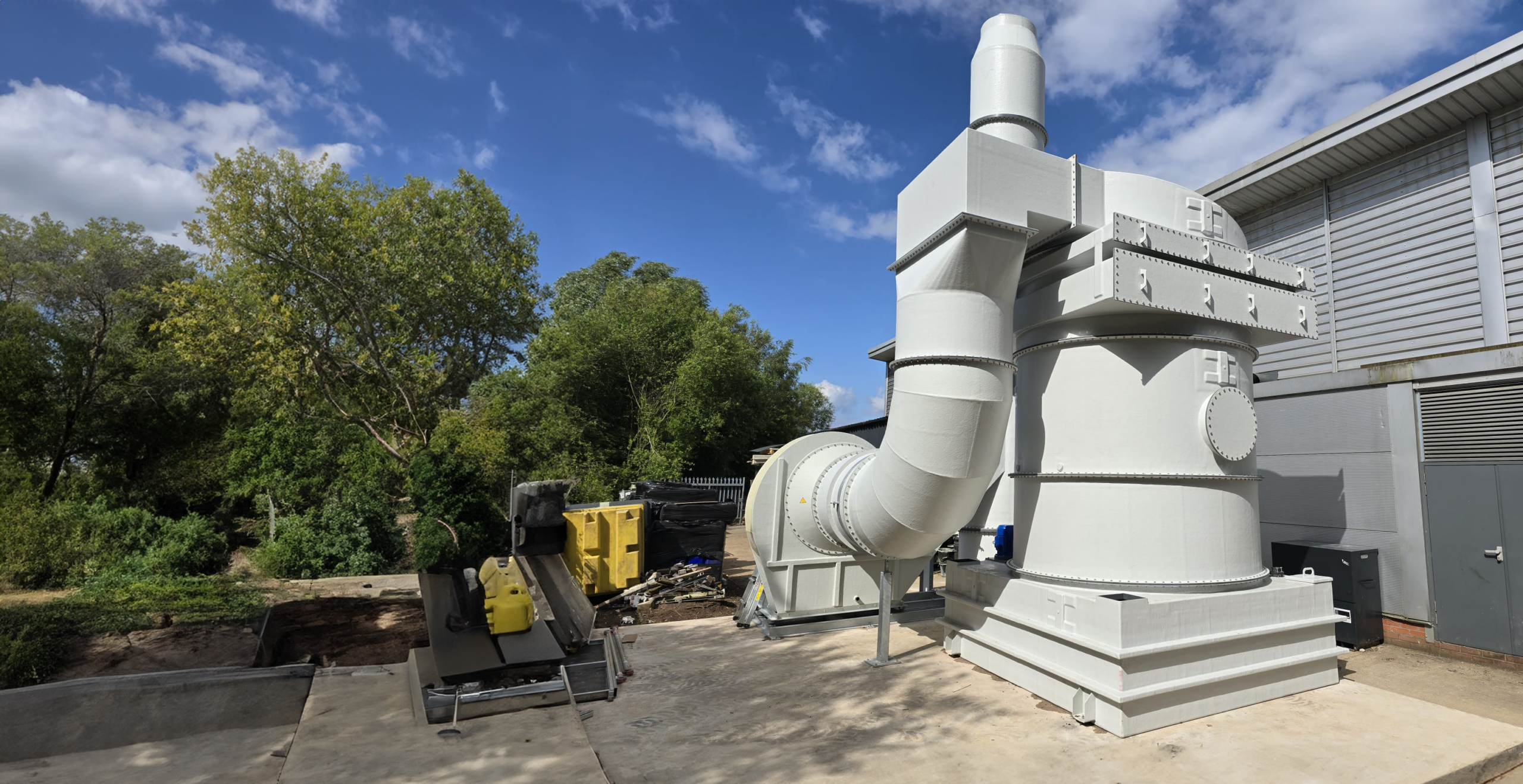
Businesses must do more than pay lip service to the green agenda
Roperhurst Managing Director, Martin Whitely calls on the industry to consider outdoor air quality as much as indoor air quality.
Rightly, there has been huge recent focus on indoor air quality (IAQ), and the importance of health and well-being within the built environment.
But we mustn’t lose sight of what our buildings discharge to atmosphere, and the steps that can be put in place to improve external air quality and our environment more generally.
IAQ matters, and so does what we discharge from buildings externally.
My company has installed fume extraction in industry for nearly fifty years. In many cases we have also designed and installed fume scrubbers to strip contaminant from the airstream.
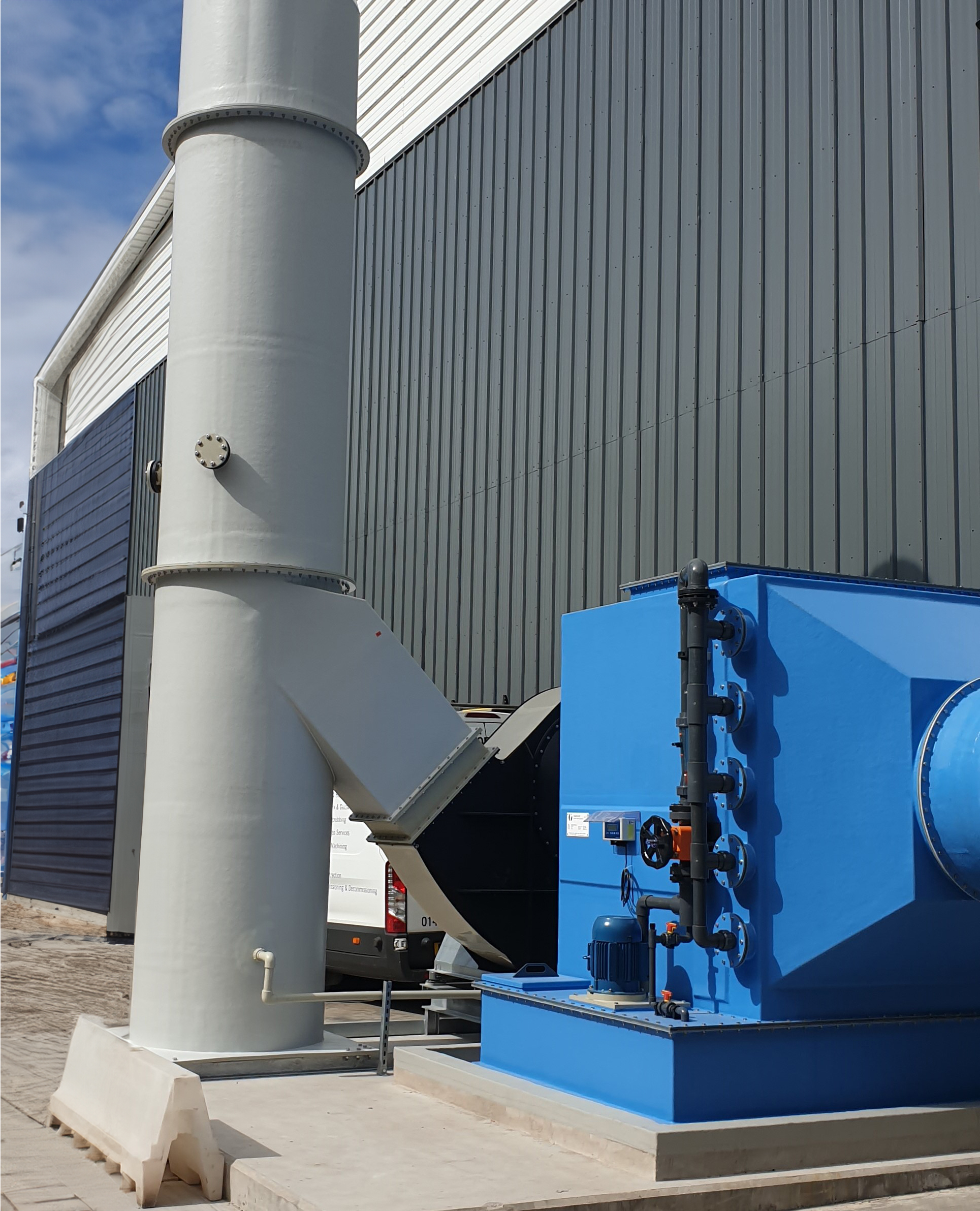
Similarly we have installed DW154 plastic fume extract ductwork in universities and hospitals across the country, but as I look back at those construction projects in the last 10 years, there are only a handful that have included one or more fume scrubbers that would have removed chemicals from emissions before discharging to air.
Out of interest, I’ve also read many universities’ sustainability and net zero plans, and all but a handful omit any mention of what they plan to do with fumes from their research activities.
And yet fume scrubbing – cleaning the nasties out of the airstream by washing or filtering the fume – has been applied for many years with great success. For example, the water industry has enormous fume scrubbing (odour control) vessels at wastewater treatment sites around the country, keeping odours at bay and preventing the release of dangerous fumes and gasses.
Population growth and a perceived lack of reinvestment has perhaps tainted the water industry’s reputation, but if their odour control wasn’t up to it, anyone living close would know about it in short order.
So what options are open to universities, hospitals and other research establishments if not quite on the scale of a wastewater treatment plant? And why do designers and consultants generally not address emissions?
Recirculatory fume hoods
Recirculatory fume hoods have become very popular in new school developments because they clean and recirculate air within a classroom or laboratory prep room without loss of heat or a change in room pressure. Because the fume cupboards are only occasionally used, a regular filter change cycle over between two and four years can mitigate the risk of fume release into the classroom environment.
But in a heavy use environment, like a university or research facility, recirculatory hoods have limited value, because operatives need assurance that the filtration works effectively each and every time.
Single fume hoods with integral scrubbing capabilities
An alternative methodology would be to fit each fume cupboard with an integral scrubbing unit, generally but not always fitted back-to-back with the fume cupboard. This has the obvious advantage that the scrubber is sized to the fume cupboard and is only in use if the cupboard is also in use.
Additionally the scrubber can be sized for the process carried out in that specific hood. Different fumes and vapours can require differing scrubbing methodologies – rather than an expensive catch all, the solution can be more targeted. Likewise, maintenance can be scheduled to fit the usage profile.
However individual scrubbers fitted to individual assets can require a substantial capital investment in large research environments with a high number of fume hoods.
Multiple fume hoods with a single fume scrubber before discharge
It is now typical for many fume hoods to be addressed by a single extract duct header, which leads to a plant room and then discharges to air via a stack. This is the model generally adopted in pharma research, semiconductors as well as university science buildings and hospitals.
In industry, typically the main header ductwork enters a fume scrubber, and fumes are scrubbed to minimise emissions. These fumes are usually scrubbed before the fan, keeping the fan internals clear of toxic and/or corrosive fumes – an important consideration for future maintenance.
Fumes could be, and sometimes are, scrubbed after the fan. This can be advantageous in that the scrubber could form part of the stack, however there is a potential hazard. Ductwork from the fan discharge to the scrubber would be under positive pressure, and our advice would always be to keep fumes within ductwork under negative pressure in case of leaks.
There is however an environmental downside in terms of energy use. Scrubbers are designed to offset a maximum load. This means that in the event that only a fraction of fume cupboards are in operation at any one time, the scrubber’s energy usage will exceed what is actually required and will therefore be inefficient.
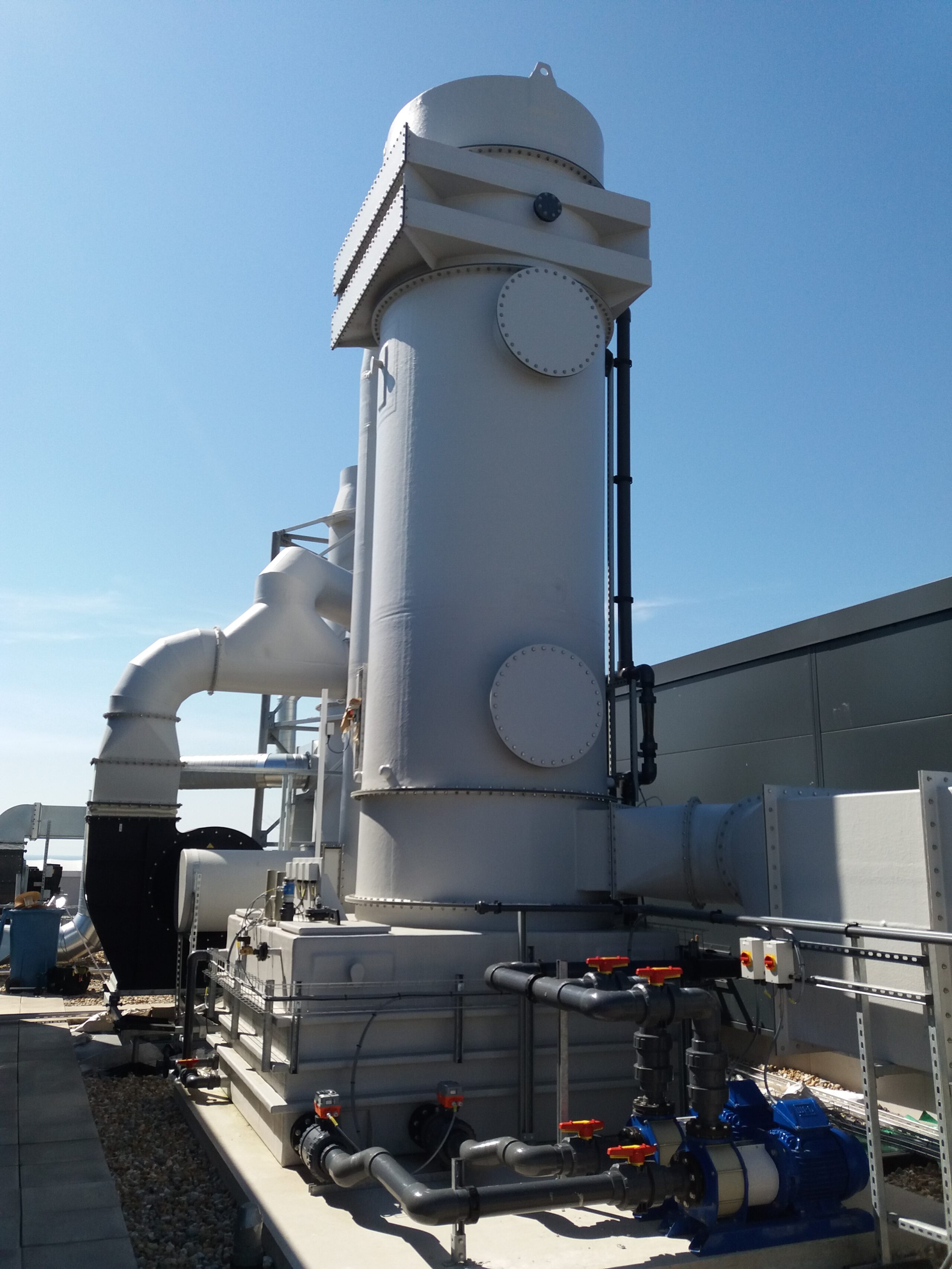
What are the considerations in fume scrubber design?
Any specification will need to consider the following:
- What is the total volume of air being moved?
- What fumes will be created by the process(es)?
- What volume of these fumes will be in the airstream?
- With what frequency?
On that basis, the scrubber designer can assess the size of scrubber, the type of packing, the type and quantity of sprays, and its pressure loss, which in turn drives fan selection.
Fume scrubber design and build are safety-critical elements of a project and must be undertaken by a specialist. In the same way that we have learned to give increased focus on internal air quality, we mustn’t lose sight of what we emit to air.