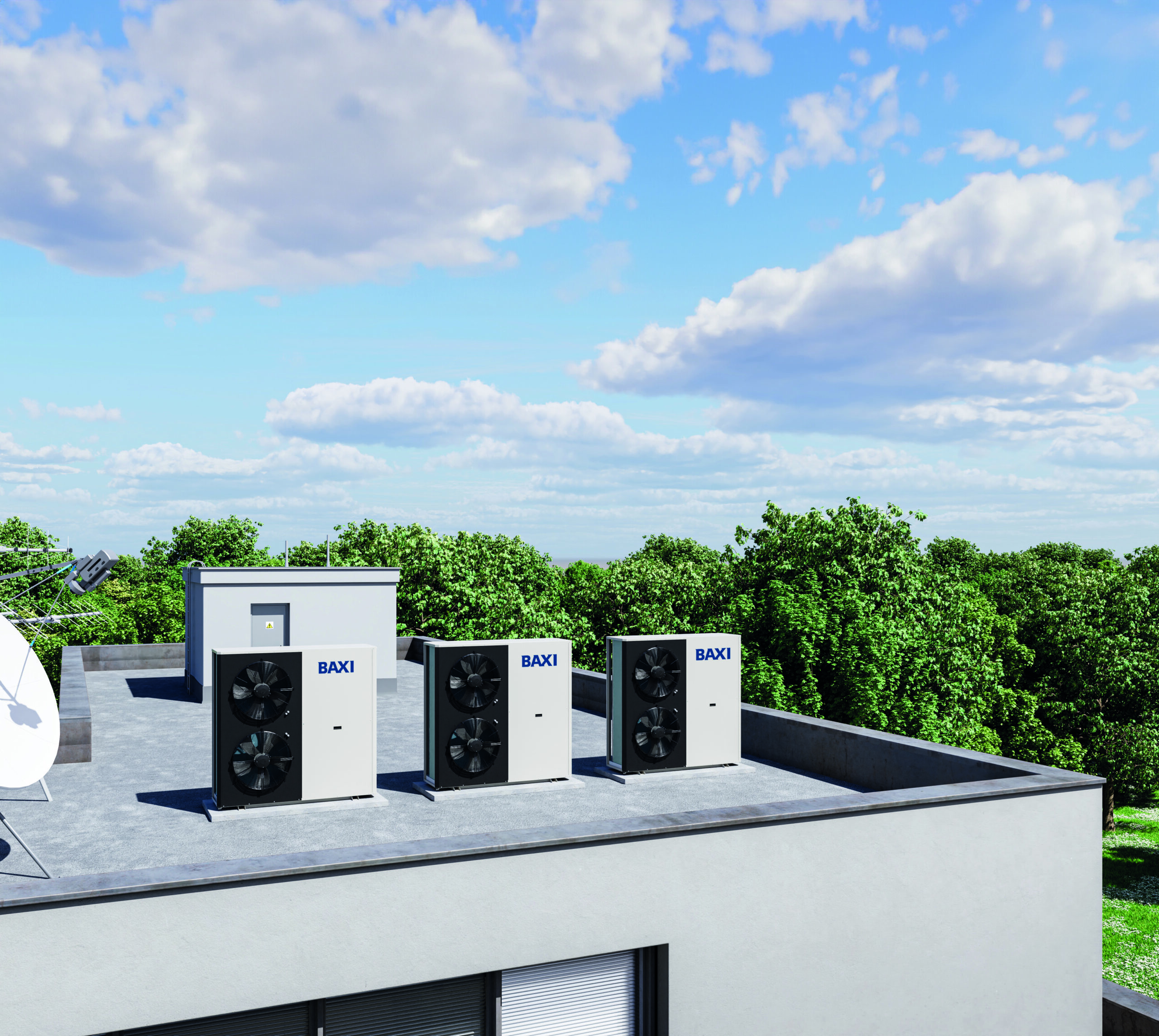
Making the switch: building system solutions
Ryan Kirkwood, Engineering Solutions Manager at Baxi, looks at key stages to consider when retrofitting heat pumps for optimal performance and energy savings.
With a 2050 net zero target enshrined in law, businesses and organisations face growing pressure to identify the fastest path to decarbonising their buildings.
Replacing traditional boilers with heat pumps provides an established route to reducing operational carbon by decarbonising heat. However, the transition is far from straightforward and requires a detailed and methodical process to achieve optimal performance and energy savings.
This involves developing a full understanding of the existing heating system, gathering real measured data, and building a series of options to enable the building owner to arrive at the best solution.
As an early stage, fabric-first upgrades should be carried out where possible to improve the building thermal envelope (see panel). But if this approach is not considered feasible, possibly due to cost or heritage considerations, what options are available to building owners wishing to decarbonise their heating?
Hybrid approach
One option might be a hybrid system, where heat pumps and boilers work together to cover the total building heating demand. There are many different design philosophies for hybrid solutions, but the aim should be to maximise renewable contribution while building a roadmap to increase utilisation.
A robust control strategy is essential to ensure maximum heat pump contribution and optimise the efficiency of both technologies. Hybrid system controls provide options for cascading up to eight heat generators – either boilers or heat pumps or a combination of the two in a hybrid installation. Your chosen solutions provider will be able to offer technical support to achieve a harmonious design that successfully blends the technologies.
High temperature heat pumps
Where the client brief is to move directly to full electrification of heat, High Temperature Air Source Heat Pumps (HT ASHPs) can meet these requirements. Yet, while they bring more flexible design options, the solution is more complex than it may seem. Replacing boilers with HT ASHPs often involves bringing the ASHP operation range into the all too familiar 82/71°C or potentially 80/60°C. This can be slightly optimistic as 80°C flow temperature for even the most modern of R290 (Propane) ASHPs is at the very top end of the performance envelope.
Even when HT ASHPs can deliver 80°C, this falls slightly short of the 82°C flow required by 82/71°C circuits. Added to which, most HPs prefer to operate in the 5-10°C ΔT range, making a straight swap on 80/60°C circuits not impossible, but challenging.
Investigative engineering
Understanding the system in full before designing a hybrid or standalone ASHP system is crucial to ensure project success.
Due to the complexity of the retrofit challenge, a degree of investigative engineering into the building profile should be carried out at the outset. The aim is to understand the actual heating demand at a system circuit level, not just the total installed capacity of the current heat generation plant.
Where design information is limited, existing meters and ultrasonic heat meters can amass real, measured data. Heat generation capacity should be recalculated, and a full heat loss calculation carried out for space heating. A comparison of the results will indicate the true building load and if temperatures can be reduced without sacrificing building comfort. This will provide a good indication of what may or may not be able to change, helping uncover new options along with any potential risks.
The data can be used to engineer a series of different solutions. This optioneering process allows clients and designers to make the best choice given any bounding constraints the project may have, such as electrical capacity, physical space or budget.
Let’s consider an example where an existing building heating system includes gas boilers operating at 82/71°C, with a 300kW constant temperature (CT) distribution system (that includes a DHW calorifier) and a 100kW variable temperature (VT) distribution system, indirectly weather compensated. Both run at the same 82/71°C boiler flow temperature. Cost and operating limitations rule out replacing emitters in the CT system, however the VT circuit emitters could be replaced to allow a lower flow temperature.
High temperature heat pumps
One approach to decarbonising this example heating system could begin with replacing the existing gas boilers with high-temperature heat pumps (HT HPs), such as the Baxi Auriga HP+, on a kW-for-kW basis. This would maintain the approximate 82/71°C operating temperature year-round, with minimal modifications to the existing circuits. However, while this method is relatively straightforward, it involves high capital costs and would push the HT HPs to their performance limits.
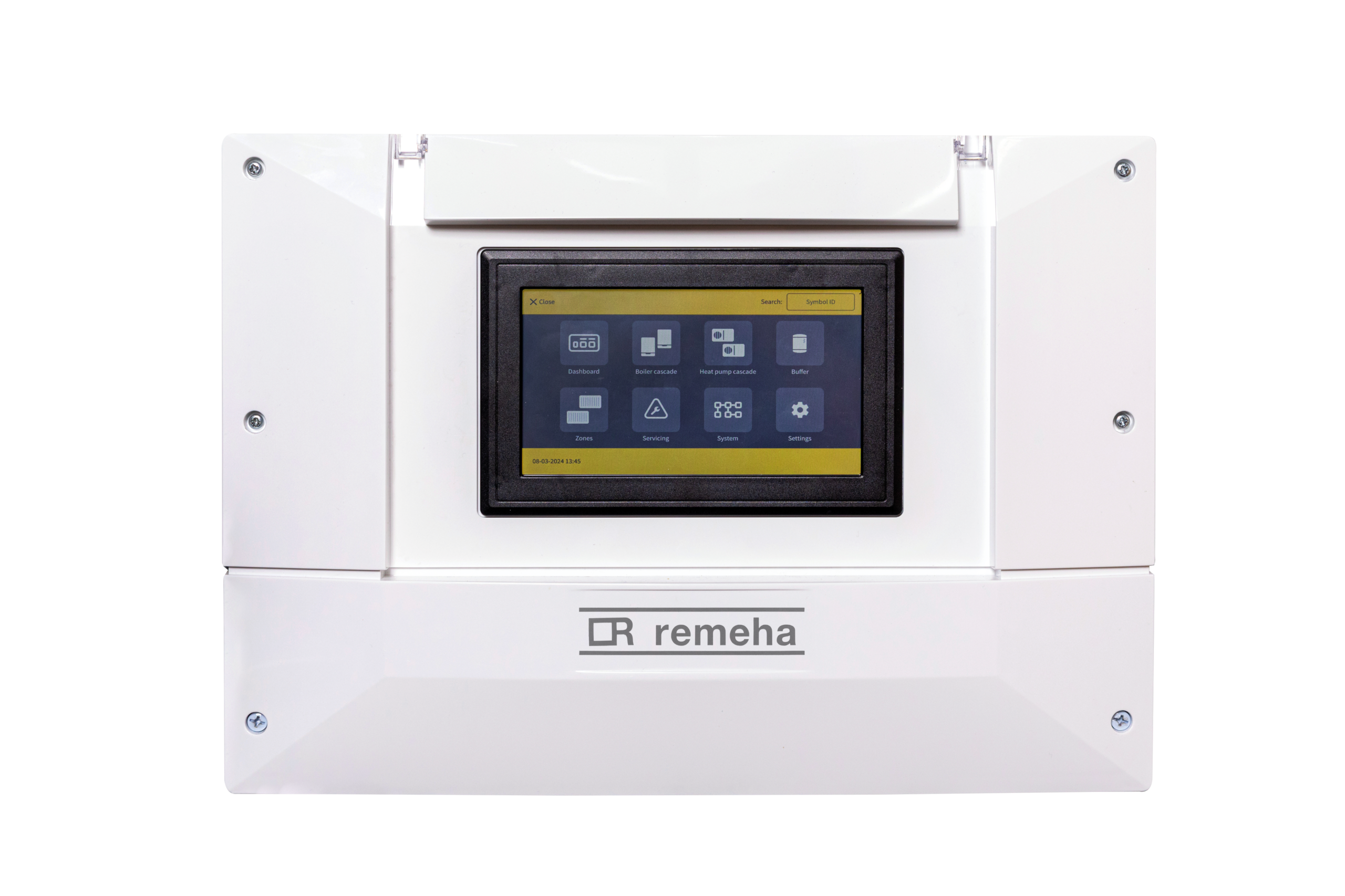
Bracketing
A more practicable solution could involve adopting a hybrid system, where the VT circuit is separated and assigned to medium or high-temperature heat pumps, while gas boilers continue to serve the CT distribution system. By consolidating the heat system and ‘bracketing’ the VT circuit, weather compensation can be handled directly at the plant, eliminating the need for mixing valves. This hybrid approach significantly reduces capital costs, lowers electrical demand, and broadens the range of heat pump technologies by lowering the flow temperature. However, it would still leave some reliance on gas boilers, only partially decarbonising the peak load.
Building up the solution
To further enhance this hybrid system, a pre-heat tank for DHW could be added, powered by an ASHP. In this setup, gas boilers remain for the CT system, while heat pumps manage both the VT circuit and DHW pre-heating. This addition decarbonises a larger portion of the heat load while still maintaining lower costs and electrical demands. However, it introduces greater complexity, requiring additional space for the DHW pre-heat tank and more advanced control systems.
This combined approach offers a path to progressively decarbonise the heating system, balancing cost-efficiency, sustainability, and system complexity.
Understanding the options
As clients begin to consider boiler replacement projects, understanding the various options for decarbonising their heating systems and the impacts of each is vital. By clearly explaining the options in a step-by-step process, expert solutions providers like Baxi can work with building services professionals to help break down the complexities for clients.
Working together, we can help set commercial buildings on their net zero journey.
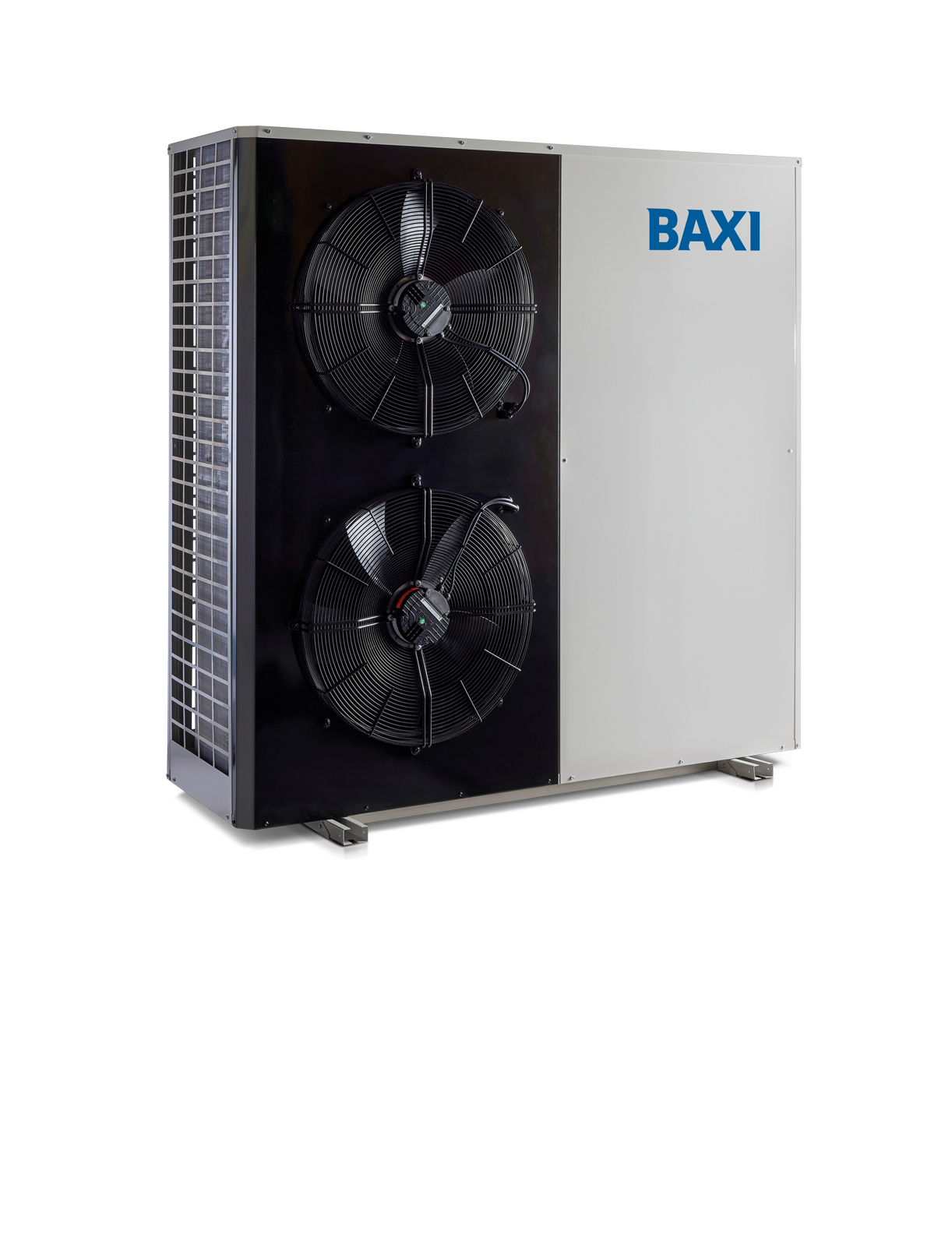
Fabric first approach
‘Fabric first’ is a term frequently used in the context of renewables, and particularly heat pumps, to refer to measures that can be taken to improve the building envelope and reduce heat losses. Any heat that is lost must be replaced, and despite the remarkable efficiencies heat pumps can offer, ensuring a cost neutral operation compared with gas boilers is still challenging. Reducing heat loss through a fabric-first approach can also considerably reduce the size of plant required for lower capital and installation costs.
However, the main reason why heat pumps are tied in with a fabric-first approach is due to flow temperatures. Air source heat pumps (ASHPs) are more efficient when the source temperature is higher and/or the sink temperature is lower. Source temperature is highly variable in the UK and not controllable, unlike the sink temperature which should be reduced when possible.
Lower flow temperatures reduce outputs from emitters designed for higher mean water temperatures (MWT). But if less heat is required due to fabric upgrades, the equation should balance itself out.